Fastener Coatings
SURFACE TREATMENTS
Surface treatments of fasteners can create great oppertunities in various applications.
Increase Corrosion Resistance
In most applications they use zinc plating or hot-dip-galvanising to increase the resistance against corrosion, but depending of the grade of the steel other treatments such as zinc-flake coatings can be applied.
#Hydrogen Embrittlement
Reduction of Friction
When a bolt is turned in a nut or treaded hole the two materials will have friction by increased tension to apply the right torque. You need to determine what maximum tension you would like to realise, in this case you can apply a surfacte treatments to reduce the friction to a known (range of) value to calculate the torque.
#Torque and Tension.
Chemical Resistance
To avoid pitting or other (electro)chemical reactions coatings can be applied to increase the chemical resistance.
Appearance or Coloring
Painting heads of screws are well known applications for coloring fasteners to it's surroundings. Facade applications and decking screws in any color is possible. Often applied together with a anti-corrosion protective base layer.
Non Electrical Conductiviness
Steel is electrical conductive by applying a non electrical conductive layer the connection will not guide current any more and is insulated. This can be used for different materials used in one construction to avoid galvanic corrosion.
Prevent from Galling
When Stainless steel fasteners are plain used galling can occur. Galling is the 'cold-welding' of a bolt and nut together. Grinding the connection off is the only way to loosen the connection.
Speeding up stainless steel fastener connections you need to apply a surface treatment to avoid galling.
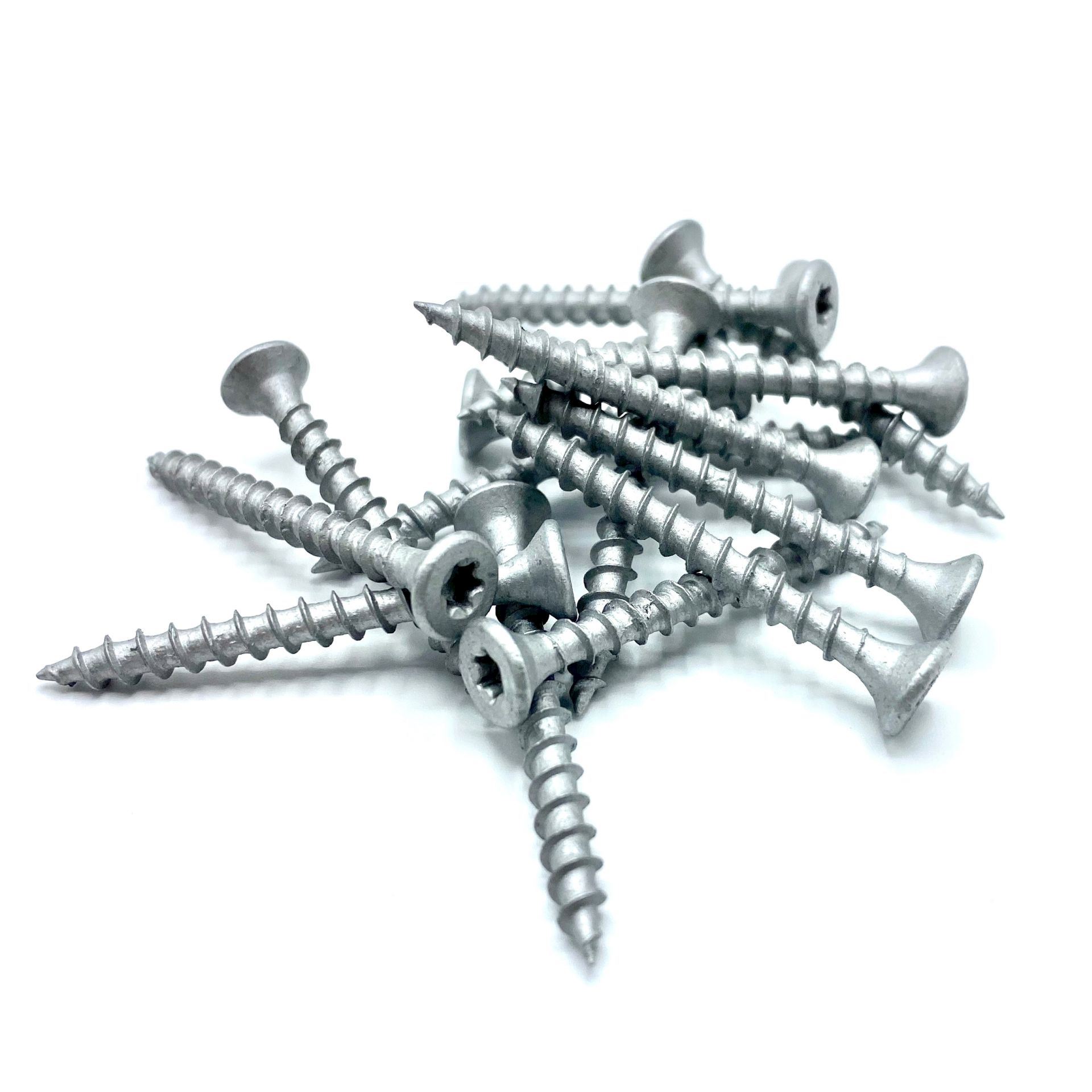
What are popular surface treatments
Please find below the most popular surface treatments in the market:
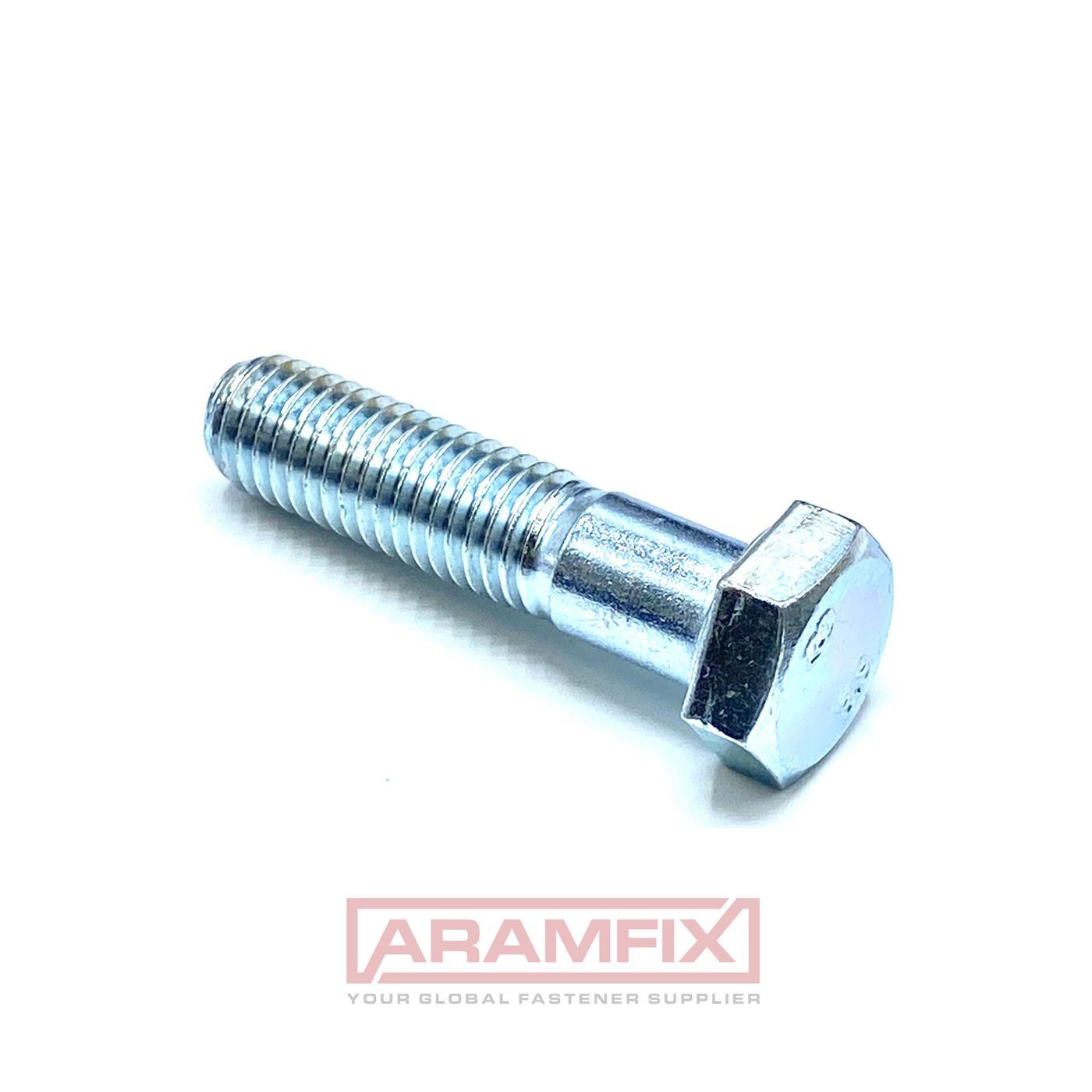
ZINC PLATING
Standard bright blue or white zinc plating is common worldwide used for many fastener applications. With a basic corrosion protection of 24hours SaltSprayTest it gives many applications for inside use. Typical layer thickness approx 3-5 microns.
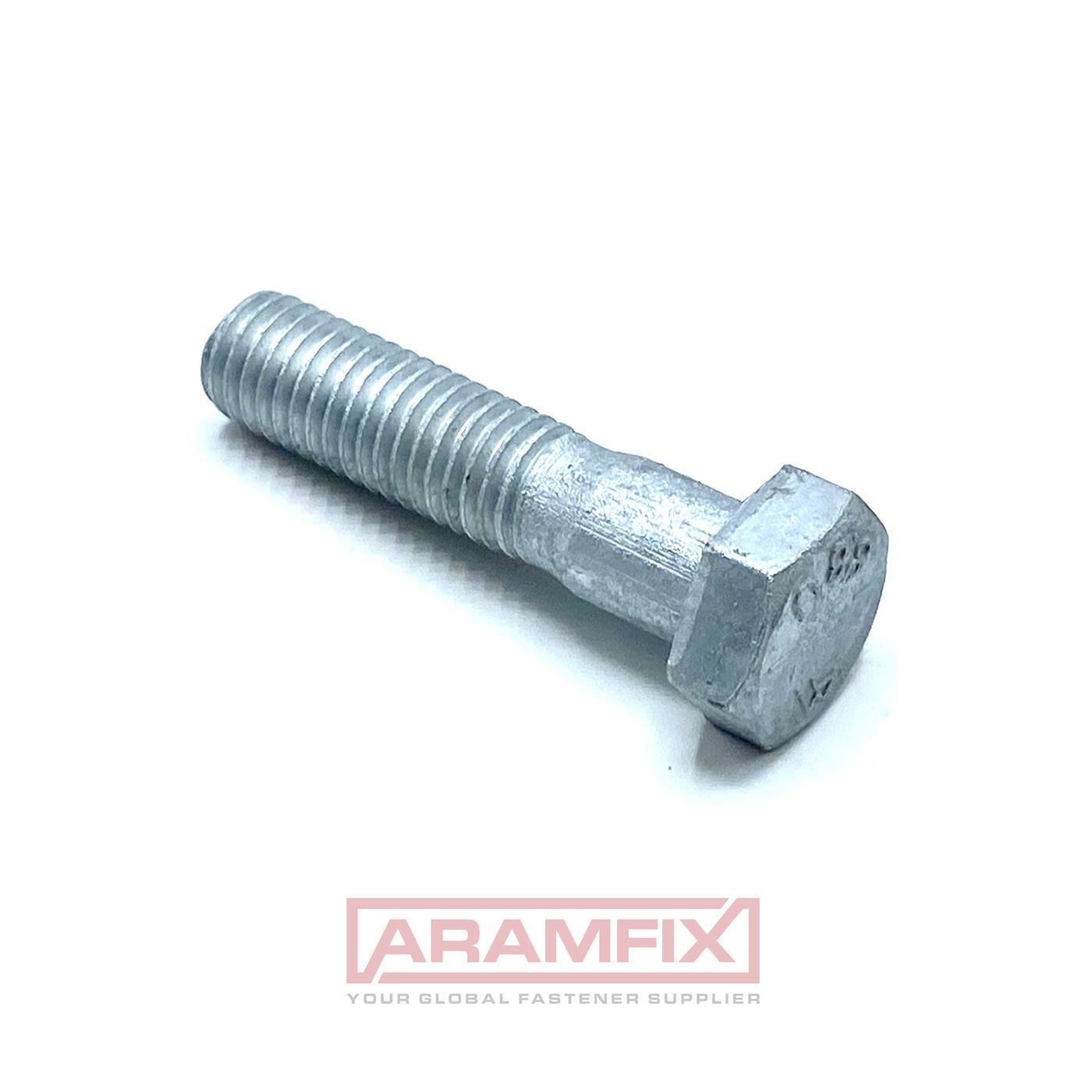
HOT DIP GALVANISING
When large constructions are hot dip galvansised often fasteners are also HDG threated. A layer of molten pure zinc in a thick layer gives great outdoor corrosion resistance. Not suitable for coastal shore area or high humidity. Typical layer thickness min 20 microns.
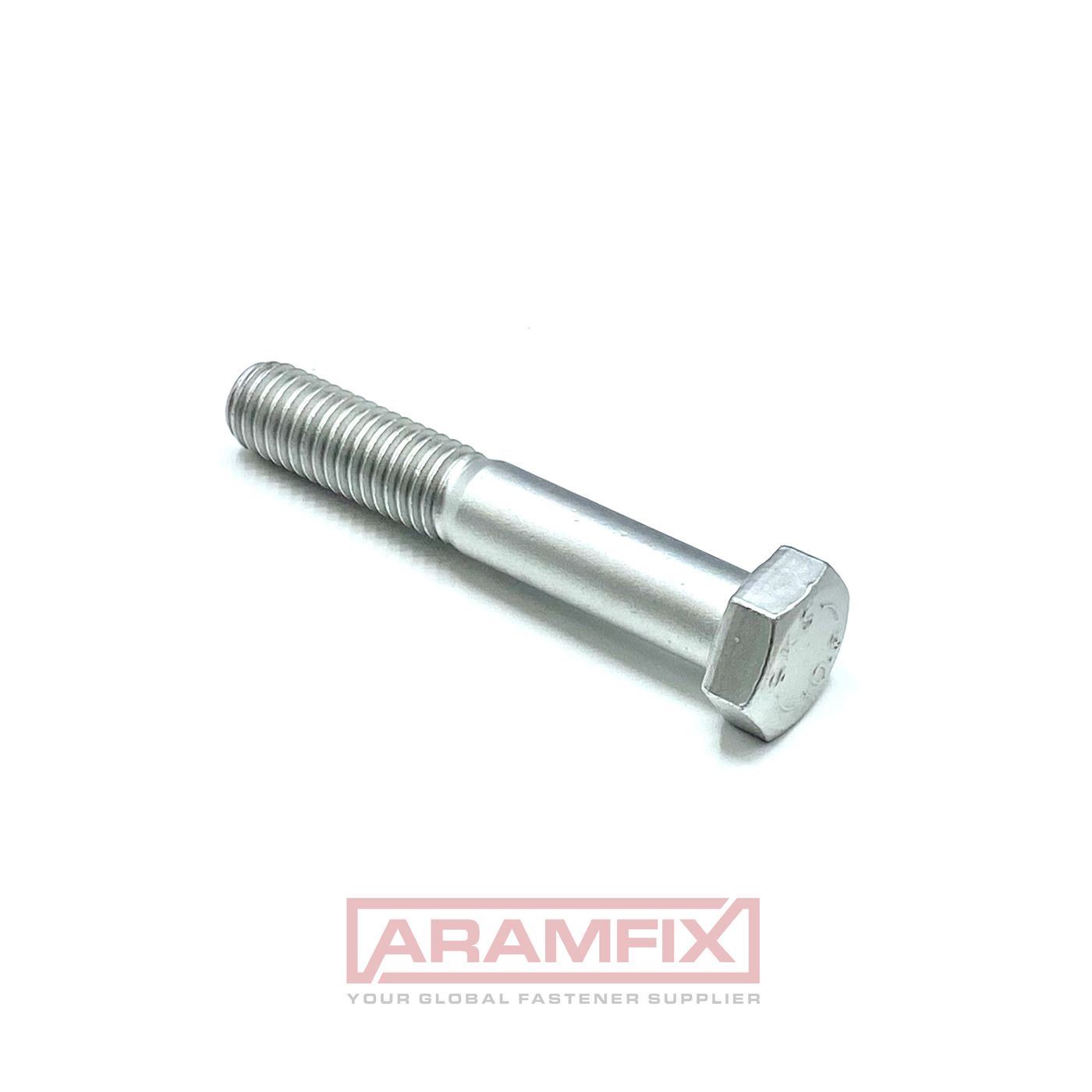
ZINC-FLAKE COATINGS
For high strength steel often zinc-flake coatings are used. There is no risk on hydrogen embrittlement so they can safely being used for steel grades with a tensile strength above 1000N/mm2. Typical layer thickness 6-10 microns.
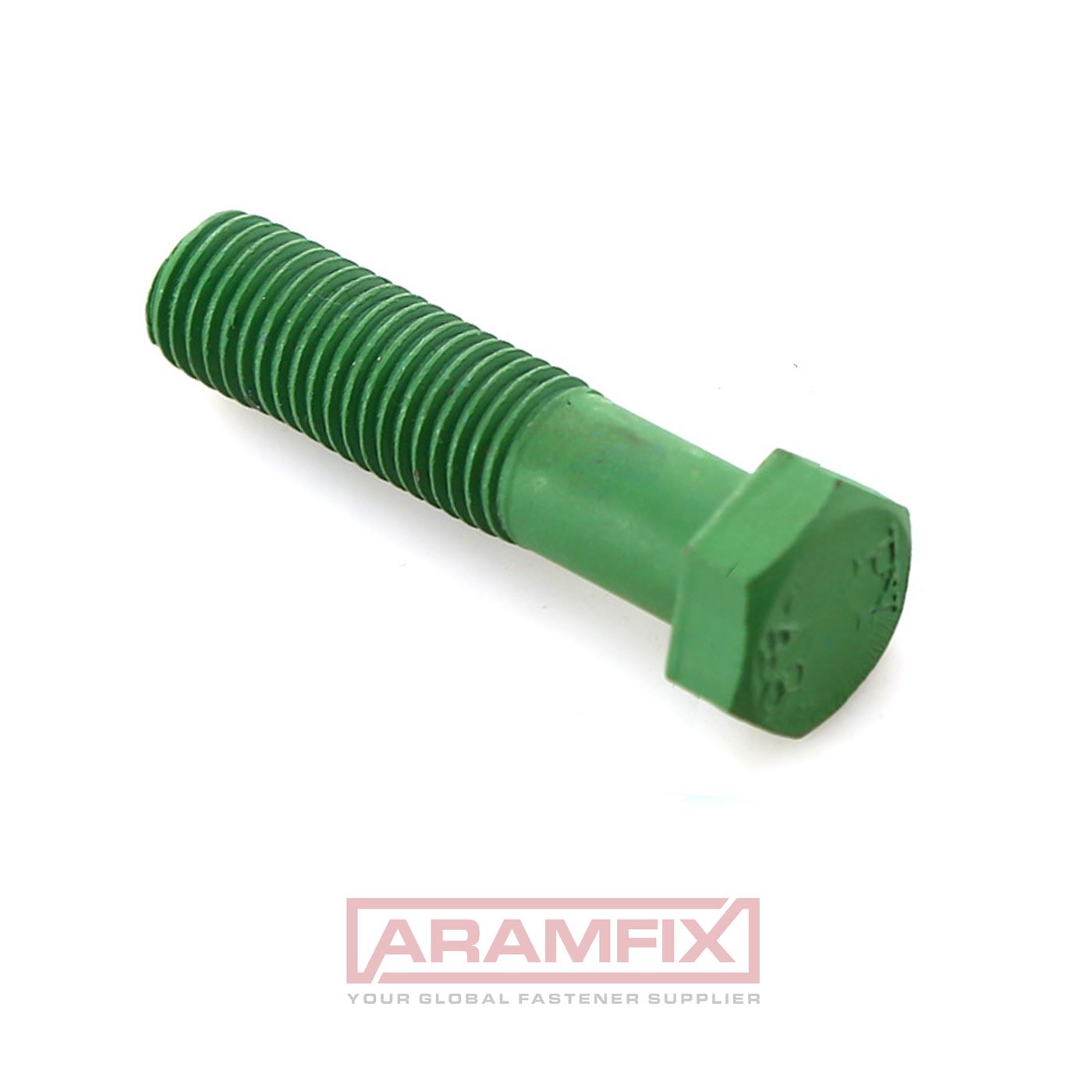
PTFE COATING
For offshore oil and gas industry often PTFE based topcoatings are used. They are in various colors available. With different base treatments a great variety of properties can be reached. Typical layer thickness above 20 microns.
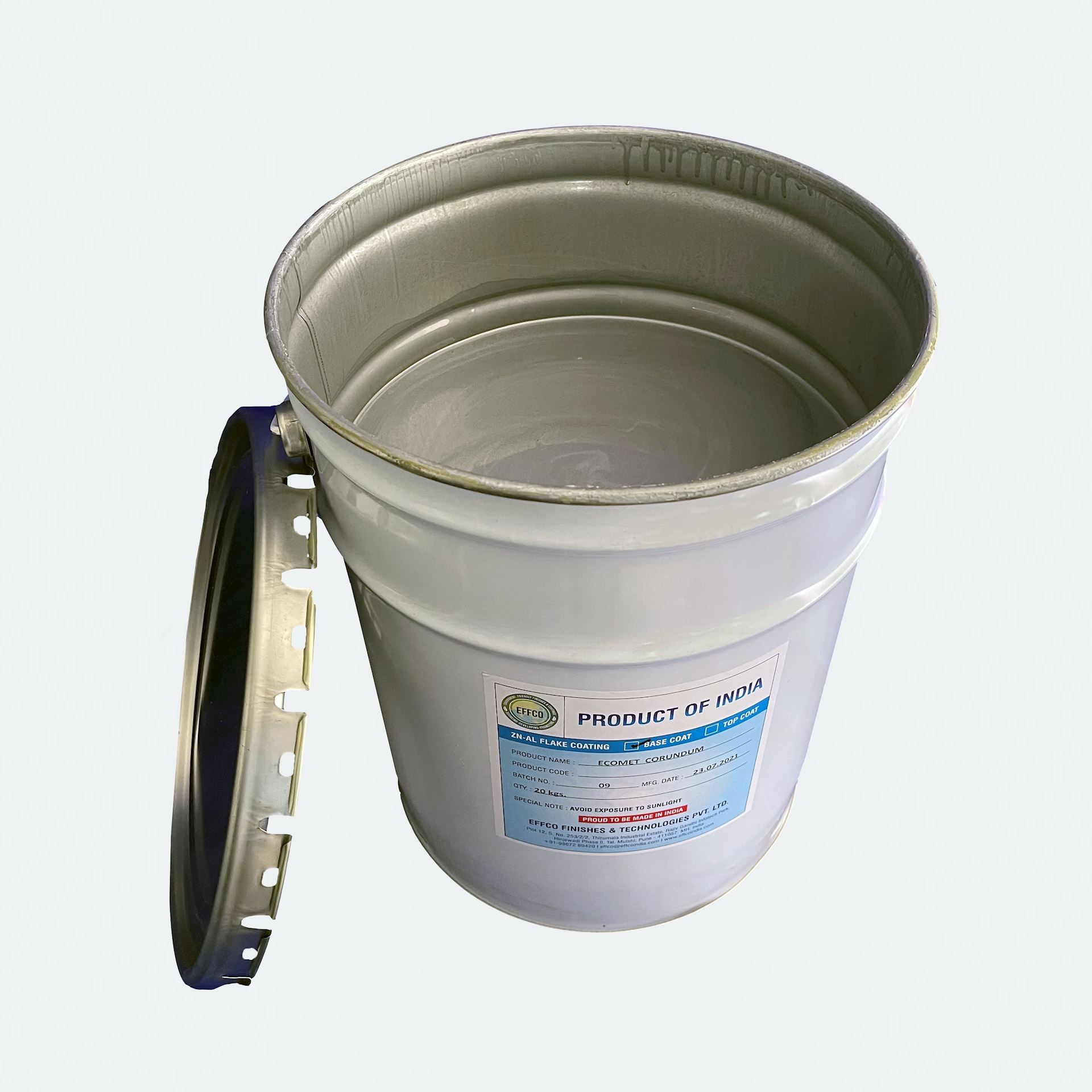
WITHOUT LICENCE
BUY ZINC-FLAKE COATING
Many Zinc-Flake coating manufacturers work with licencees. In every country there is one or some more job-coaters who may pay for the licence to buy their coating to apply commercially on fasteners. Since 2008 the Indian manufacurer EFFCO FINISHES & TECHNOLOGIES PVT. LTD. developed high corrosion resistant zinc-flake coatings water- or solvent-based. Now they have started to sell this licencee-free. To have this technology available for any manufacturer or as added value to small production batches. ARAMFIX made it possible to order online the products and equipment of EFFCO FINISHES & TECHNOLOGIES PVT. LTD.
FAQ
-
Is it necessary to order a full container?
No, it is not necessary to order a full container. Depending on the product, desired delivery date etc. your order can also be shipped seperatly.
-
What is the minimum order quantity?
This is depending on the product and the minimum order qtty set by the manufacturer.