Austenitic stainless steel grades
Austenitic stainless steel is one of the five classes of stainless steel by crystalline structure (along with ferritic, martensitic, duplex and precipitation hardened. Its primary crystalline structure is austenite (face-centered cubic) and it prevents steels from being hardenable by heat treatment and makes them essentially non-magnetic. This structure is achieved by adding enough austenite stabilizing elements nickel, manganese and nitrogen.
There are two subgroups of austenitic stainless steel. 300 series stainless steels achieve their austenitic structure primarily by a nickel addition while 200 series stainless steels substitute manganese and nitrogen for nickel, though there is still a small nickel content.
300 series stainless steels are the larger subgroup. The most common austenitic stainless steel and most common of all stainless steel is Type 304, also known as 18/8 or A2. Type 304 is extensively used in such items as, cookware, cutlery, and kitchen equipment. Type 316 is the next most common austenitic stainless steel. Some 300 series, such as Type 316, also contain some molybdenum to promote resistance to acids and increase resistance to localized attack (e.g. pitting and crevice corrosion).
SAE designation are similar to the AISI designations. For example: SAE 304 is similar as AISI 304.
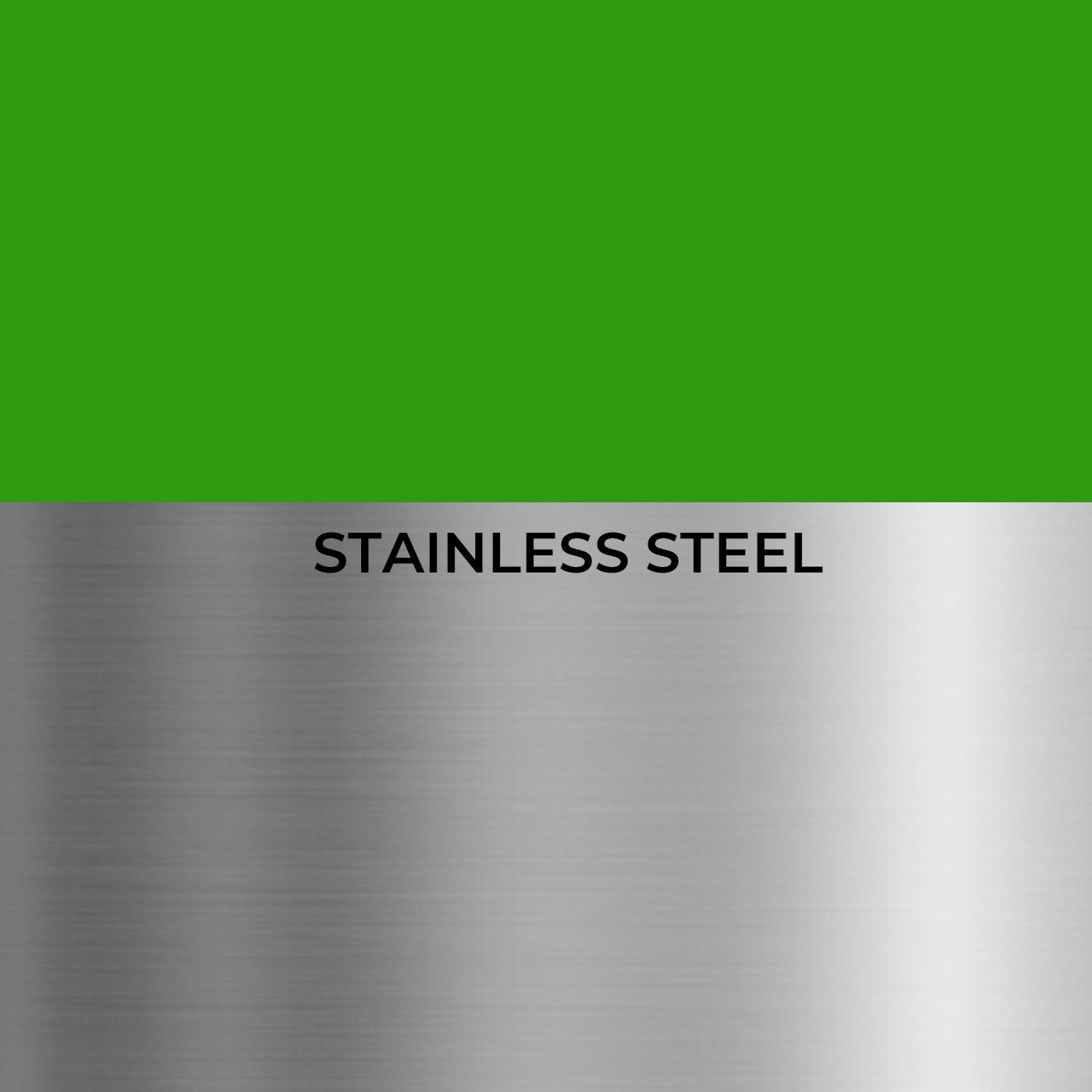
AISI 304 stainless steel
SAE or AISI 304 stainless steel is the most common stainless steel. The steel contains both chromium (between 18% and 20%) and nickel (between 8% and 10.5%) metals as the main non-iron constituents. It is an austenitic stainless steel. It is less electrically and thermally conductive than carbon steel and is essentially-magnetic but less magnetic than steel. It has a higher corrosion resistance than regular steel and is widely used because of the ease in which it is formed into various shapes.
The composition was developed by W. H. Hatfield at Firth-Vickers in 1924 and was marketed under the trade name "Staybrite 18/8”. It is specified by SAE International as part of its SAE steel grades. Outside the US it is commonly known as A2 stainless steel, in accordance with ISO 3506 for fasteners. In the commercial cookware industry it is known as 18/8 stainless steel. In the unified numbering system it is UNS S30400. The Japanese equivalent grade of this material is SUS304. It is also specified in European norm 1.4301.
Corrosion resistance
304 stainless steel has excellent resistance to a wide range of atmospheric environments and many corrosive media. It is subject to pitting and crevice corrosion in warm chloride environments and to stress corrosion cracking above about 60 °C. It is considered resistant to pitting corrosion in water with up to about 400 mg/L chlorides at ambient temperatures, reducing to about 150 mg/L at 60 °C.
304 stainless steel is also very sensitive at room temperature to the thiosulfate anions released by the oxidation of pyrite (as encountered in acid mine drainage) and can undergo severe pitting corrosion problems when in close contact with pyrite- or sulfide-rich clay materials exposed to oxidation.
For more severe corrosion conditions, when 304 stainless steel is too sensitive to pitting or crevice corrosion by chlorides or general corrosion in acidic applications, it is commonly replaced by 316 stainless steel.
Difference between 304, 304H and 304L
They all possess the same nominal chromium and nickel content and thus possess the same corrosion resistance, ease of fabrication and weldability.
The carbon content of 304H (UNS S30409) is restricted to 0.04–0.10%, which provides optimal high temperature strength.
The carbon content of 304L (UNS 30403) is restricted to a maximum of 0.03%, which prevents sensitization during welding. Sensitization is the formation of chromium carbides along grain boundaries when a stainless steel is exposed to temperatures in the range of approx. 900–1,500 °F (480–820 °C). The subsequent formation of chromium carbide results in reduced corrosion resistance along the grain boundary leaving the stainless steel susceptible to unanticipated corrosion in an environment where 304 would be expected to be corrosion resistant. This grain boundary corrosive attack is known as intergranular corrosion.
The carbon content of 304 (UNS 30400) is restricted to a maximum of 0.08%. Thus 304 is not useful for corrosive applications where welding is required such as tanks and pipes where corrosive solutions are involved, thus, 304L is preferred. And its lack of a minimum carbon content is not ideal for high temperature applications where optimal strength is required, thus, 304H is preferred. Thus 304 is typically restricted to bars that will be machined into components where welding is not required or thin sheets that are formed in articles such as kitchen sinks or cookware that are also not welded.
Carbon content has a strong influence on room temperature strength and thus the specified minimum tensile properties of 304L are 5 kilopounds per square inch (34 MPa) lower than for 304. However, nitrogen also has a strong influence on room temperature strength and a tiny addition of nitrogen produces 304L with the same tensile strength as 304. Thus, practically all 304L is produced as dual certified 304/304L, meaning it meets the minimum carbon content of 304L and also meets the minimum tensile strength of 304.
Color code for threaded rods/studs: RAL6024 Traffic Green
AISI 316 stainless steel
SAE or AISI 316 grade stainless steel, sometimes referred to as A4 stainless steel or marine grade stainless steel, is the second most common austenitic stainless steel after 304/A2 stainless steel. Its primary alloying constituents after iron, are chromium (between 16–18%), nickel (10–12%) and molybdenum (2–3%), with small (<1%) quantities of silicon, phosphorus & sulfur also present. The addition of molybdenum provides greater corrosion resistance than 304, with respect to localized corrosive attack by chlorides and to general corrosion by reducing acids, such as sulfuric acid. 316L grade is the low carbon version of 316 stainless steel. When cold worked, 316 can produce high yield and tensile strengths similar to Duplex stainless grades.
It is commonly used in chemical and petrochemical industry, in food processing, pharmaceutical equipment, medical devices, in potable water, wastewater treatment, in marine applications and architectural applications near the seashore or in urban areas.
Color code for threaded rods/studs: RAL3000 Flame red.
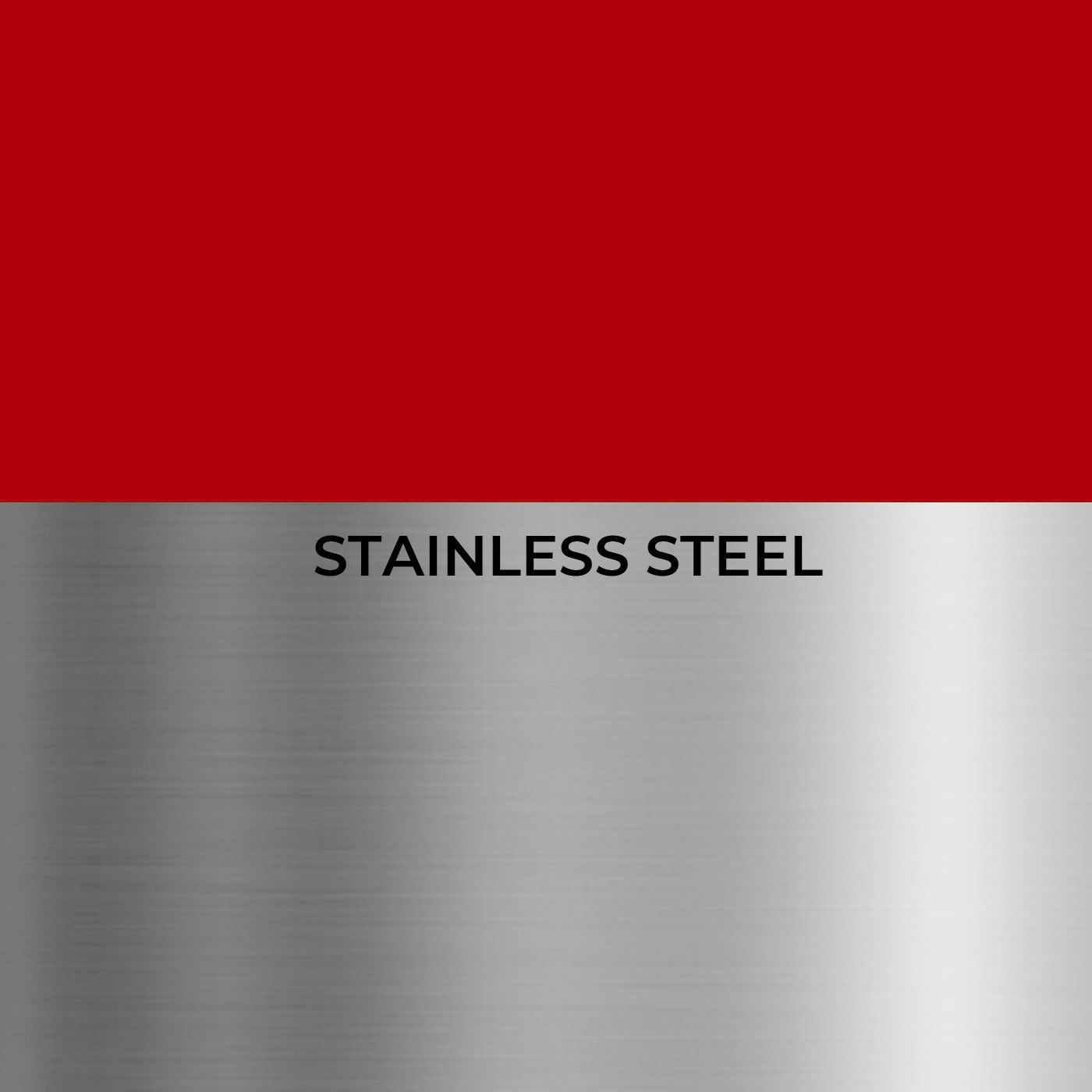