FAQ
Here is a Glossary all about fastener related topics.
-
Glossary A.
A SHEET METAL SCREWS - Sheet metal screws (AKA Tapping Screws) with (a) sharp-pointed ends: and (b) fewer threads per inch than type AB screws; and (c) deeper threads with better gripping power than type AB. The IFI incorrectly labels the type A an obsolete thread thought it is universally preferred in 18-8 stainless steel over type AB, especially by the marine industry.
A2 - The most commonly produced grade of stainless steel, grade 304 and is the notification as a metric fastener. It contains 18% Chromium and 8% nickel, thus commonly called 18-8 Stainless Steel. A2 is an austenitic steel and is non-magnetic. The chromium provides a corrosion and oxidation resistance, however, it can tarnish. Stainless steel A2 property classes for fasteners are 50, soft or 70 cold-worked.
A286 - This is an iron-based superalloy which features an austenitic structure with high amounts of nickel and chromium. A286 (or Incoloy) is ideal for high strength and corrosion resistance up to 704 degrees C and for lower stress applications at high temperatures. Low temperature capabilities including ductility, non-magnetic, high strength at -196 degrees C
A325 - Heavy Hex Head Structural Bolts
A4 - Stainless steel grade 316 and a notification for metric fasteners. Commonly used in marine applications where you need more corrosion resistance. Adding molybdenum (2-3%) to the mix provides this extra resistance. A4 grade is austenitic, non-magnetic , the molybdenum increases the corrosion resistance to withstand attack from many industrial chemicals and solvents and chlorides. A4 grade stainless steels come in property classes : 50, soft and 80 high-strength.
A490 - Heavy Hex Structural Bolts
A574 - Strength Grade for socket head cap screws
AAR - Association of American Railroads
AASHTO - American Association of State Highway and Transportation Officials
AB MODE - An abbreviation for Alternate Blow Mode. A machine feature that allows for the feeding of the wire on every other machine stroke. This allows for the forming of some higher load parts on a given machine size.
AB SHEET METAL SCREWS - Sheet metal screws with pointed ends similar to type-A and dimensions similar to type B sheet metal screws. Type AB has more threads per inch than the Type A Sheet Metal Screw.
ABRASIVE - NATURAL - (Sandstone, emery, corundum, diamonds) or artificial (silicon carbide, aluminum oxide) material used for making grinding wheels, sandpaper, abrasive cloth and lapping compounds.
ABS - Plastic material, a class of plastic based on acrylonitrile-butadiene-styrene copolymers.
AC - Active Coils
ACCEPTABLE QUALITY LEVEL (AQL) - The acceptable quality level is a nominal value expressed in terms of percent defective, i.e. defects per hundred units by which a group of sampling plans is identified. The AQL is specified for each individual characteristic and is not cumulative.
ACCEPTANCE NUMBER (Ac) - The acceptance number is the maximum number of defects for a specific characteristic in any given sample resulting in the acceptance of the lot.
ACCURATE - Conforms to a standard or tolerance
ACI - American Concrete Institute
ACME THREAD - A thread form which has a 29 degree thread angle with a thread height half of the pitch, the apex (or crest) and valley (root) are flat. Used in applications for feed or adjusting screws on machine tools.
ACORN DIE - A form of threading die for use in screw machines. The cutting portion resembles an acorn.
ACQ - Pressure treated lumber is treated with Alkaline Copper Quaternary (ACQ) an environmentally friendly water-based preservative that is free of arsenic and chromium.
ACR - Anti Cam-out Ribs on the Phillips II drive recess to improve drive bits from cam-out during the installation phase. There are ribs on the drive bit that engage the fastener recess to reduce stripping, provide increased torque, enhance off-angle drivability, and offer a stick fit that makes screw driving easier.
ACR PHILLIPS II PLUS - ACR Phillips II Plus is a screw-drive design that can be driven by a #2 Phillips driver or a #2 Robertson driver, but when driven by a Phillips II Plus bit, the combination results in a stick-fit interface.
ACTIVE COILS - (Also known as effective coils of working coils) - The number of coils which are free to move when the spring is loaded.
ACUTE ANGLE - An angle that is less than 90 degrees.
ADAPTER - A tool holding device for fitting together various types or sizes of cutting tools to make them interchangeable on different machines.
ADDITIONAL AGENT - A material added in small quantities to a solution to modify its characteristics or the properties of the deposit obtained from the solution.
ADHESION - The strength of the bond between a coating and its substrate which is measured as the force per unit area required to separate them
ADHESIVE ANCHOR - Typically, a threaded rod or rebar that is installed in a predrilled hole in a base material with a two-part chemical compound.
ADHESIVE BONDING - The joining of two or more materials through the use of adhesives such as liquids, drops or gels.
ADVANCED TRIM HEAD - The AXIS wood screw Trim Head is slightly larger in diameter than industry standards. This combined with the patent pending Turbine Ribs gives maximum holding power while leaving a clean, professional finish.
ADVANCING KICKOUT - A machine mechanism (normally found on Single Die Double Stroke Rivet Headers) where the die kickout pin moves forward between the cone and finish blows to expose material to be upset into the head
AESTHETIC DESIGN HEAD - Head is shaped to fit a neat design in cabinetry on ETX wood screws
AGE HARDENING - A process of aging that increase hardness and strength and ordinarily decreases ductility. Age hardening usually follows rapid cooling or cold working.
AGING - A spontaneous change in the properties of a metal usually associated with the recovery of metal from an unstable condition produced by quenching or by cold working (strain aging). Age hardening and Aging are terms commonly used synonymously. See Precipitation Hardening.
AIR HARDENING - (Air Quenching) A hardening process wherein the steel is heated to the hardening temperature and cooled in air. Unless steel is high in carbon or alloy, it will not show much increase in hardness when air hardened. Mainly used with tool steels and stainless steel. Modern air-hardening steels are characterized by low distortion during heat treatment because of their high-chromium content. Their machineability is good and they have a balance of wear resistance and toughness.
AIR-LIFT HAMER - A type of gravity drop hammer that uses an air cylinder to raise the ram and deliver blows to a forging. Because the velocity can be controlled, each blow can vary based on the amount of force needed to properly forge a metal.
AIR-LIFT HAMMER - A type of gravity-drop hammer in which the ram is raised for each stroke by an air-cylinder. Because of the length of stroke can be controlled, ram velocity and therefore the energy delivered to the workpiece can be varied. Also see Drop Hammer and Gravity Hammer.
AIRCRAFT QUALITY - Stock and forgings used for aircraft applications including Aerospace that require close monitoring during production. This helps reduce flaws both on the surface and internally as well as cracks, inclusions, and segregations of the forging.
AIRCRAFT QUALITY FASTENERS - To be used in highly stressed applications, are to be produced under closely controlled, special and in most cases restricted methods of manufacture and inspection.
AISC - American Institute of Steel Construction. A technical institute and trade association established to serve the structural steel design community and construction industry in the United States.
AISI - The American Iron and Steel Institute. An association of North American steel producers developed in response to the need for a cooperative agency in the iron and steel industry for collecting and disseminating statistics and information, doing investigations, providing a forum for a discussion of problems and generally advancing the interest of the industry.
ALIGNMENT PLUG - A tooling component used to represent a formed part during the setup of the transfer fingers in the external setup fixture. These plugs change to suit the part diameter being gripped.
ALKALINE - The ionic substance that has a pH value greater than 7. A base that dissolves in water and acts as an electrolyte in the presence of metal.
ALKALINE BLACKENING (BLACK FINISHING) - Producing a black oxide coating on steel by immersion in hot alkaline salt solutions.
ALKALINE CLEANING - Cleaning by means of alkaline solutions.
ALL-METAL - Often refers to locknuts which have no nylon inserts. These nuts are effective under harsh temperatures and extreme corrosive conditions.
ALLEN WRENCH - Commonly referred to as a hex key or an Allen key. This tool is used to drive internal hex socket screws and other hexagonally shaped socket fasteners.
ALLOWABLE LOAD - The maximum design load that can be applied to an anchor. Allowable loads for mechanical and adhesive anchor are based on applying a factor of safety to the average ultimate load.
ALLOWABLE LOAD - The maximum permissible load in a structural part or assembly. As applicable, it can be specified strength of the hardware (e.g., in a fastener specification): a statistically based, lower-bound, load carrying capacity derived from the test data; or the load derived from the allowable stress of the materials.
ALLOWABLE STRESS DESIGN (ASD) - A design method in which an anchor is selected such that service loads do not exceed the anchor's allowable load. The allowable load is the average ultimate load divided by a factor of safety.
ALLOWANCE - A specific amount of clearance or interference between threads. Also an intentional difference between the maximum material limits of mating parts. It is a minimum clearance (positive allowance) or maximum interference (negative allowance) between such parts.
ALLOWANCE - The prescribed difference in dimensions of mating parts to provide a certain class of fit
ALLOY - A material with metallic properties composed of two or more elements at least one of which is a metal. A steel that contains a small amount of various alloying elements including silicon, molybdenum, manganese, vanadium, nickel, titanium, copper, chromium, and aluminum. Alloys change the performance of the steel in strength, corrosion resistance and other properties demanded by the application.
ALLOY - A metal formed by a mixture of two or more different metals
ALLOY 20 - This alloy has approximately 20% Chromium and 34% Nickel plus 3% to 4% Molybdenum. It is very corrosion resistant and is especially popular when in contact with sulfuric acid.
ALLOY 600/625 - High Temperature Alloy
ALLOY 718/722/ X-750 AM350 - High Temperature Alloy
ALLOY DEPOSITION - Co-deposition of two or more metals.
ALLOY STEEL - A steel containing elements, other than carbon, which have been added to obtain definite mechanical or physical properties, such as higher strength at elevated temperatures, toughness, etc.
ALLOY STEEL - Steel which contains in addition to the normal elements of iron, carbon, and manganese, one or more elements in sufficient quantity to impart improved mechanical properties. The small amounts of elements and impurities such as sulfur, silicon, phosphorus, and aluminum which are usually present in any steel are not considered alloys. If manganese is added to steel in sufficient quantity, it may be considered as an alloy in alloy steel.
ALLOY STEEL - A mixture (or alloy) of ordinary steel added to other metals besides carbon with the specific purpose of attaining certain characteristics such as higher strength. A few exceptions to this definition exist, however, so that a chromium content above 4% is not considered alloy steel and above 12% is considered stainless steel.
ALLOYING ELEMENTS - Chemical elements combined with a metal in order to alter and improve the properties of the base metal.
ALUMINUM - An element with the atomic number 13. This material is known for its excellent strength to weight ratio and is used widely in metal. Aluminum is blueish and silvery-white, very light, malleable, and ductile with high heat and electrical conductivity. It is non-magnetic and one-third the weight of steel with good corrosion resistance against certain chemicals and acids but weak resistance against other elements such as sea water.
AMS - Aeronautical Material Specifications are material and process specifications for aircraft components confirming to established engineering and metallurgical practices in the aircraft industries. They were developed by the SAE Aeronautics Committee.
AMSLER - Swiss manufacturer of fatigue testing machines. The Amsler Vibrophone, a high frequency electro magnetic resonance machine, is used extensively for fatigue testing by the fastener industry.
AN SPECIFICATIONS - Dimensional standard for aircraft fasteners developed by the aeronautical standards group. All drawings are prefixed by AN.
ANAEROBIC ADHESIVE - An adhesive which hardens in the absence of air, such adhesives are often used as a thread locking medium.
ANCHOR BOLTS - A steel rod or bar with one end intended to be embedded in concrete and the other end threaded and projected for anchoring material to concrete. The end cast in concrete may be straight, bent hook, a forged head or welded attachment to resist forces imposed on the anchor bolt.
ANCHOR CATEGORY - The classification for an anchor that is established by the performance of the anchor in reliablility tests such as sensitivity to reduced installation effort for mechanical anchors or sensitivity to hole cleaning for adhesive anchors.
ANCHOR SPACING - The distance from centerline to centerline between two anchors.
ANGLE CONTROLLED TIGHTENING - Method of tightening where the person installing the fastener removes the slack from the assembly, and then tightens the fastener a prescribed amount (e.g. 120 degrees) based on the length of the fastener. This method is often coupled with the use of torque for the initial "snug" tightening
ANGLE CONTROLLED TIGHTENING - A tightening procedure in which a fastener is first tightened by a pre-selected torque (called the snug torque) so that the clamped surfaces are pulled together, and then is further tightened by giving the nut an additional measured rotation. Frequently bolts are tightened beyond their yield point by this method in order to ensure that a precise preload is achieved. Bolts of short length can be elongated too much by this method and the bolt material must be sufficiently ductile to cater for the plastic deformation involved, Because of the bolt being tightened beyond yield, its re-use is limited.
ANGLE NUTRUNNER TOOL - Angle nutrunners are well suited for many assembly applications. The minimal dimensions of angle heads allow them to reach into restricted places. which longer effective length reduces the torque reaction forces on the handle. For higher torque applications, these tools can be fitted with torque reaction devices.
ANGLE OF GRIND - Angle subtended by the ground and surface of the spring.
ANGLE OF HEAD - In countersunk heads, the included angles of the conical under portion or bearing surface, usually 82 degrees or 100 degrees. Standard metric countersunk screws have a head angle of 90 degrees.
ANGULAR RELATIONSHIP OF ENDS - The relative position of the hooks or loops of tension springs, or the legs of a torsion spring, to each other.
ANGULARITY - The angle between the axis of two surfaces of a fastener.
ANION - A negative charged ion.
ANNEAL - Subjecting to high heat, with subsequent slow cooling to remove effects of cold working, to soften material hardened in heat treatment, to increase ductility and relieve stress; heating metal to a temperature above the critical range, holding it at that temperature a sufficient length of time for it to be heated through its full volume, and slowly cooling it through the critical range: cooling may be performed by cooling the metal slowly in the furnace, or by allowing it to cool to room temperature.
ANNEALED - A fastener is considered in the annealed state when it has been heated and cooled to make it soft - that is, free from hardness (stresses) caused by working or previous heat treatment. Also refines it structure or changes it ductility, toughness, or other properties.
ANNEALING - A heat treating process in which an iron-based metal is fully austenized and allowed to cool slowly, thereby relieving stress and often decreasing strength properties while increasing the ductility.
ANNEALING - The controlled heating and cooling of a metal to remove stresses and to make it softer and easier to work with.
ANNULAR FETTER - Assymetrical thread form with sharp crest and root-annular are ground and helical are milled Straight faced (angle or duplex) or single faced Gimlet.
ANODE - The material in a corrosive attack that becomes corroded.
ANODE - (1) in electrolysis, the electrode at which negative ions are discharged, positive ions are formed, or other oxidizing reactions occur. (2) The object which is intended to perform these functions.
ANODE BAGGING - Some anodes (e.g. Nickel anodes) are put in a cloth bag, before suspension in solution, so that the insoluble particles from the anode are collected in the bag instead of falling into the solution.
ANODE CORROSION - Dissolution of anode metal by the electrochemical action in the plating cell.
ANODE EFFICIENCY - Current efficiency of a specified anodic process.
ANODE FILM - (1) The thin layer of a solution which is in contact with the anode and differs in composition from the bulk of the solution. (2) Solid film formed on the anode during operation.
ANODIC (REVERSE) CLEANING - Electrolytic cleaning in which the work piece is the anode.
ANODIC COATING - (1) A metallic coating on a metal surface, the metal of the coating being less noble compared to that of the base meatal. (Sacrificial coating). (2) A protective, decorative, or functional coating, formed by conversion of the surface of a metal in an electrolytic oxidation process (See Anodizing)>
ANODIZING - The formation of an oxide film on the surface by means of an anodic treatment. This is commonly used on aluminum. Acid electrolytic treatment with frosty-etched appearance. Hard oxide surface gives excellent protection and reduced porosity. Tempered alloys can be dyed any color Type 1, Class 2. Good paint base and good for close tolerance parts.
ANODIZING (ANAODIC OXIDATION) - An electrolytic oxidation process in which the surface layer of a metal is converted to a coating having protective, decorative, or functional properties.
ANOVA - An abbreviation of analysis of variance.
ANSI - American National Standards Institute establishes the "Unified Screw Thread Standards" which regulates the fastener thread industry.
ANSI/ASME NOMENCLAURE (B1.1 & ALL) - The various "B" numbers are standards set by ASME regarding various aspects of fasteners. The most common number B1.1, deals with dimensions and thread tolerances; B1.2 with gages and their use; B1.3 with various systems for gaging threads; B1.7 with definitions of terms.
ANTI-FRICTION COATING (AF) - AF coating are dry lubricants consisting of suspensions of solid lubricants, such as graphite, PTFE, or molybdenum disulphide of small particle size in a binder. Such coatings can be applied to fastener threads to replace metallic coatings such as zinc and cadmium and offer maintenance free permanent lubrication. By careful selection of the lubricants, AF coatings can be designed to meet specific applications. The coatings are permanently bonded to the metal surface and provide a lubricating film preventing direct metal to metal contact.
ANTI-SEIZE COMPOUND - An anti-seize compound is used on the threads of fasteners in some applications. The purpose of the compound depends upon the application. It can prevent galling of mating surfaces - such compounds are frequently used with stainless steel fasteners to prevent this effect from occurring. In some applications it is used to improve corrosion resistance to allow the parts to be subsequently dis-assembled. Thirdly, it can provide a barrier to water penetration since the threads are sealed by use of the compound.
ANVIL - The head or tail of the fastener which is in contact with the outer surface of the joint material.
ANVIL - The part of an installation tool nose assembly used to swage the collar of a lockbolt fastener. Commonly known as a swaging anvil.
APPLIED FORCE - A measure of the user applied force as the screw is installed. More force is not necessarily better.
APPLIED LOAD - Force or moment transferred across a joint; it does not include preload or changes in preload as a result of temperature change. (NOTE: APPLIED LOAD is also referred to in literature as External load, Externally Applied Load or Service Load)
ARBOR - That portion of a lathe carriage that contains the clutches, gears, and levers for moving the carriage. It also protects the mechanism.
AS FORGED - The condition of a forging as it comes out of the finisher cavity without any subsequent operations.
ASD - Allowable Stress Design (According to the AISC 9th Ed.)
ASME - American Society of Mechanical Engineers. The organization is known for setting codes and standards for mechanical devices.
ASSEMBLY - A unit of fitted parts that make up a mechanism or machine.
ASTER RECESS - The ASTER recess was designed by LISI Aerospace to provide a more reliable solution than the hexagonal recess for assemblies on composite structures on aircraft. The recess is optimized to fit on the threaded end of aerospace fasteners. These fasteners allow for tightening the nut and holding the bolt simultaneous, on the same side of the structure, by only one operator.
ASTM - Specifications Standards developed by the American Society for Testing and Materials.
ASTM 193-194 - ASTM 193 are chemical and physical specifications for hex hex cap screw, studs, and bolts made of steel and stainless steel. ASTM 194 refers to nuts. The commonly used stainless is called grade 8, referring to 304 material to certain specifications, and grade 8M referring to 316 material. The major differences between ASTM and commercial stainless fasteners are: (a) 304 material must be used for manufacturing grade 8, not simply 18-8: (b) ASTM generally refers to heavy hex head and heavy nuts, though semi-finished hex heads and finished nuts may be supplied with the permission of the buyer; (c) cold formed material will require carbide solution treatment or annealing to reduce hardness to meet ASTM requirements.
ATHREADED INSERT - An insert for installation into sheet material where a receptacle for a male-threaded component is required.
AUSTEMPERING - A patented heat-treating process that consists of quenching an iron based alloy from a temperature above the transformation range in a medium having a high rate of heat abstraction, and then maintaining the metal until transformation is complete, at a substantially uniform temperature which is below that of pearlite formation and above that of martensite.
AUSTENITE - A solid combination of iron and at least one alloying element defined by a cubic crystal structure that is face-centered. Most common engineering steels transform into pearlite, bainite, or martensite during the austenite phase when factoring in the cooling rate.
AUSTENITE - A phase in steels which consists of the gamma form of iron with carbon in solid solution. Austenite is tough, non-magnetic and tends to work-harden rapidly when cold worked in those steels which are austenitic at ordinary temperatures. A specific metallic solution of steel that allows for higher carbon absorption. Austenite exists in the temperature range of approximately 1341 F (727C) to 2719 F (1493C). It is non-magnetic, has the crystal structure of face-centered cubic.
AUSTENITIC - Refers to 300 series stainless steel, the most popular of the stainless alloys accounting for 85%-90% of stainless fasteners sold. Named for Sir Robert Williams Austen, an English metallurgist, austenitic stainless is a crystal structure formed by heating steel, chromium and nickel to a high temperature where it forms the characteristics of 300 series stainless steel. An AUSTENITE is a molecular structure where 8 atoms of iron surround one atom of carbon, thus limiting the corrosive effects of the carbon. Austenitic fasteners have the highest level of corrosion resistance in the stainless family, cannot be hardened by heat treatment, and are non-magnet for practical proposes. The most popular of austenitic grades is known generically as 18-8 stainless, and grades 302, 302HQ, 303, 304, 305, and XM-7. Typical industries using 18-8 stainless fasteners include: food, dairy, wine chemical, pulp and paper, pharmaceutical, boating swimming pools, pollution control, electronic, medical and hospital equipment, computer, and textile. Type 316 stainless has added nickel and especially molybdenum. The molybdenum (called moly) sharply increases corrosion resistance to chlorides and sulfates, including various sulfurous acids in the pulp industries has superior tensile strength at high temperatures compared to 18-8. Besides pulp and paper, typical industries using 316 are: photographic and other chemicals, ink, textile, bleach, rubber. Exotic metals in the 300 series include 309, 310, 317, 321, and 347. With superior resistance at elevated temperatures, these metal are used for furnace parts, high temperature containers and processing equipment, aircraft parts such as collector rings, exhaust systems, and equipment for very corrosion compounds of sulfuric, nitic, citric and lactic acids.
AUSTENITIC STEEL - A steel which has a stable austenitic structure at normal (room) temperatures, or 300 series, stainless steels. They contain a maximum of 0.15 percent carbon, a minimum of 16 percent chromium and sufficient nickel and/or manganese to retain an austenitic structure at all temperatures from the cryogenic region to the melting point of the alloy.
AUSTENIZING - The process of uniformly hearing a metal until the grain structure transforms from Ferrite to Austenite. For carbon steels, transformation begins at approximately 1341 degrees F and becomes completely uniform throughout the metal at a higher temperature (varies by carbon content).
AUTOCATALYTIC PLATING - Deposition of a metallic coating by a controlled chemical reduction that is catelyzed by the metal or alloy being deposited.
AUXILIARY OPERATIONS - Additional processing steps performed on forgings to obtain properties, such as surface conditions or shapes, not obtained in the regular processing operation.
AVERAGE COATING THICKNESS - This is determined as either the value obtained by analytical methods or the mean value of a specified number of local thickness measurements that are evenly distributed over the significant surface.
AWS - American Welding Society
AXIAL LOAD - Force applied through the axis of a fastener or structure.
AXIAL ROLLS - In ring rolling, vertically displaceable, tapered rolls, mounted in a horizontally displaceable frame opposite from but on the same centerline as the main roll and rolling mandrel. The axial rolls control the ring height during the rolling process.
AXIS/AXIS OF THREAD - Axis of the pitch cylinder.
AXISYMMETRIC FORGING - A forging where metal flow, during deformation, is predominately in a direction away from a common axis in a radial direction.
-
Glossary B.
B - When followed by a number (ex: B-90), hardness measured on the Rockwell Scale.
B - When referring to sheet metal screws, Type B indicates a blunt point with more threads per inch and smaller thread depth than a Type A sheet metal screw.
BACKING OFF - Loosening of a nut over time by spinning back up the thread.
BACKSIDE PROTRUSION - Protrusion of a fastener from the back side of the work piece. May apply to protrusion either before or after installing the fastener.
BACKWARD EXTRUSION - Forcing metal to flow on a direction opposite to the motion of a punch or die.
BACKWARD EXTRUSION - When metal is contained in a die or punch insert and forced to flow around a penetrating punch or pin. Typically applies to the forming of a hole in a workpiece.
BAKING - The process of heating fasteners for an extended period of time preferably within one hour after electroplating. This is done to reduce the risk of hydrogen embrittlement. Stress Relieving of parts that are over a hardness of HRc 30 that have had an electroplating operation.
BAKING OF CASE HARDENED PARTS - Electroplated fasteners which are case hardened should be baked for a minimum of four hours within the temperature range of 375-450 degrees F, no later than four hours after the plating process. This baking process does not guarantee that hydrogen embrittlement will not still be present after baking or that it will not occur at a later date while in service. Specialized testing or a substitute part may be required depending on the application.
BALL LOCK TYPE DRIVING TOOL - This retention design uses a ball and spring tension method to secure sockets to an extension or adaptor. Tools can typically be removed by hand allowing for quick changes.
BANDING - Segregation of alloying elements in a metal, seen as parallel bands, in the direction of rolling.
BAR - A section hot rolled from a billet to a form, such as round, hexagonal, octagonal, square or rectangular, with sharp or rounded corners or edges, with a cross-sectional area of less than 16 sq in. (A solid section that is long in relation to its cross-sectional dimensions, having a completely symmetrical cross section and whose width or greatest distance between parallel faces is 3/8 inches or more.
BAR CODING - Machine readable alphabetic and/or numeric information used for identification of packaged parts.
BAR END - See End Loss.
BARREL - Long cylindrical portion of a fastener. Most used about a cylindrical portion of a standoff.
BARREL PLATING - A particular example of barrel processing by which electrodeposits are applied to articles in bulk: in contract to vat plating in which articles are individually suspended during the electrodeposition process.
BARREL PROCESSING - Mechanical, chemical or electrochemical treatment of articles in bulk in a rotating container. Examples: barrel burnishing, barrel polishing, barrel cleaning.
BARREL TUMBLING - Process in which parts to be deburred are put together with abrasive material into a barrel and rotated for prolonged periods for the purpose of burr removal.
BARRELING - Convexity of the surfaces of cylindrical or conical bodies, often produced unintentionally during upsetting or as a natural consequence during compression testing.
BARRIER PROTECTION - A method of fighting corrosion in which a layer of inert material (e.g. paint) is placed over the fastener to prevent rust.
BASE MATERIAL - The concrete, brick, or block material into which an anchor is placed.
BASE METAL - Opposite of noble metal. (Not to be confused with basis metal). Examples of base metals are aluminum, magnesium, zinc, cadmium, iron, etc.
BASIC SIZE - That size from which the limits of size are derived by the application of allowances and tolerance.
BASIC THREAD PROFILE - This is the theoretical profile of external and internal threads with no manufacturing tolerance applied.
BASIS MATERIAL - Material upon which coatings are deposited or formed (Not to be confused with base metal).
BATCH/BATCH-TYPE FURNACE - A furnace for heating materials where all loading and unloading is done through a single door or slot.
BDC OR B.D.C. - An abbreviation for Back Dead Center. This is when the heading slide is at the opposite end of the forming stroke, furthest from the face of the dies.
BEARING STRESS - The surface pressure acting on a joint face directly as a result of the force applied by the fastener.
BEARING SURFACE - The supporting or locating surface of a fastener (head or tail) with respect to the part which it fastens (mates). The loading of a fastener is usually through the bearing surface. Washers are commonly used to increase the bearing surface. A part of a fastener such as the washer face on a nut or under the head of a hex head cap screw that actually comes in contact with the part it fastens.
BEARING-TYPE JOINT - A bolted connection that assumes that shear forces are transmitted by the bolt bearing against the sides of the holes in the connected material. Often denote on drawings with an (X) (i.e. A-325-X) which excludes threads from the shear plane on (N) (i.e. A325-N) which includes threads in the shear plane.
BED - A stationary and rigid structure, typically constructed from metal, to which the bolster plate of metal stamping equipment is attached.
BED CUSHION - A plate or series of vertically moving plates mounted below the bolster plates of a press. The cushion helps regulate the metal flow by controlling the blank force.
BELL MOUTH - A slightly conical shape at the front of a tooling impression
BEND OR TWIST (DEFECT) - Distortion similar to warpage, but resulting from different causes; generally caused in the forging or trimming operations. When the distortion is along the length of the part, it is called (BEND), when across the width, it is called (TWIST).
BEND RADIUS - The radius of a bent pipe, tube, sheet, or cable measured from the inside curvature. It can also be defined as the minimum radius that an element can bend without kinking or sustaining damage.
BEND RELIEF - Clearance notch at an end of flange to allow bending without distorting or tearing adjacent material.
BEND TEST - A test commonly made by bending a cold sample of specified size through a specified circular angle. Bend tests provide an indication of the ductility of the sample.
BENDER - A die impression, tool, or mechanical device designed to bend forging stock to conform to the general configuration of die impressions subsequently to be used.
BENDING - Generally applied to forming. Creation of a formed feature by angular displacement of a sheet metal workpiece. A preliminary forging operation to give the piece approximately the correct shape for subsequent forming. Also note Drawing and Forming.
BENDING FORCE - A force that acts to bend a component putting one side of the part in tension and the opposite side in compression. Bending forces have the same units as torque, but instead of twisting a part in-line with its longitudinal axis, bending forces can be applied in any orientation. Typically, these are described as prying or eccentric forces for fasteners.
BEST WIRE SIZE - The diameter of a wire that will contact the thread flank at the pith diameter. Best wire size can be calculated from thread pitch and flank angle using simple geometry.
BEVEL - A surface not at right angles to the rest of the piece. A small slant, usually describing a flat washer which is square and thicker on one side than the other. The slant of the beveled washer can offset a slanted surface, so that a bolt going into a beveled washer may be parallel to the ground.
BI-HEXAGON HEAD - A bolt or screw whose cross section of its head is in the shape of a 12 pointed star.
BILLET - A semi-finished, cogged, hot-rolled, or continuous-cast metal product of uniform section, usually rectangular with radiused corners. Billets are relatively larger than bars.
BINDING HEAD - Rounded top surface and slightly tapered sides. The bearing surface is flat, with annular undercut optional.
BITE - Amount of the die in contact with the workpiece throughout one entire forging reduction, e.g. heavy bite is three-quarter to full width of the die.
BLACK BOLTS & NUTS - The word black refers to the comparatively wider tolerances employed and not necessarily to the colour of the surface finish of the fastener.
BLACK NICKEL - Generally used as a matching finish without lacquer coating.
BLACK OXIDE - A "Conversion Coating" which means it is formed by a chemical reaction with the metal to form an integral surface, as opposed to an "Applied Coating" which bonds with the metal. An oil finish is applied as a rust inhibitor. No risk of hydrogen embrittlement. An attractive black finish.
BLACK PHOSPHATE - Standard finish on retaining rings, drywall and particle board screws. Color is dull black to a bright black appearance.
BLACK PHOSPHATE & OIL - Standard coating on black phosphate. Non-drying petroleum oil is 1100 mg per sq/ft minimum. Oil serves as a rust inhibitor and a lubricant. Some fasteners with this plating call out required salt-spray test. Common fasteners include frame bolts, spring nuts, floorboard screws and Grade GT locknuts.
BLACK ZINC - A shiny black appearance with fair rust resistance qualifies.
BLACKENING - Black finishing: Black Oxide
BLANK - Raw material or forging stock (also called a slug or multiple) from which a forging is made.
BLANK - (1) A specific length of stock after being sheared from the coil of wire. (2) A part while in the process of being formed. (3) A formed but not yet completed part. Example: Screw Blank
BLANK - A fastener in some intermediate stage of manufacture. The material has been cut to weight or length and is used to create forged parts, also known as forging stock.
BLANK - (1) Sheet metal stock from which a product is to be made. (2) Workpiece resulting from blanking operation. By stoking blanks, a fastener manufacturer can meet a variety of fastener orders.
BLANKING - Die cutting of the outside shape of a part.
BLAST CLEANING - A process for cleaning or finishing metal objects by use of an air jet or centrifugal wheel that propels abrasive particles (grit, sand, or shot) against the surfaces of the workpiece at high velocity.
BLASTING - A process in which particles are projected at high velocity against the work piece.
BLIND APPLICATION - Structure with access from only one side, requiring fasteners that can be fully installed from the exposed side.
BLIND FASTENER - A fastener that can be placed with access to only one side of the application.
BLIND HOLE - A hole which can only be accessed from one end.
BLIND INSERT - A straight, cylindrical insert pressed into a case with a mating counterbore. The insert does not go all the way through the case.
BLIND RIVET - A rivet designed for use where only one side of the work is accessible. A two-part fastener with a mandrel and a body (eyelet).
BLIND SIDE - The side of the joint, which cannot be accessed (e.g. the inside surface of a tubular or box section).
BLIND-SIDED HOLE - A type of hole that does not go completely through the material. Most screws are assembled into blind-threaded holes.
BLOCK - The forging operation in which metal is progressively formed to general desired shape and contour by means of an impression die (used when only one block operation is scheduled).
BLOCK AND FINISH - The forging operation in which the part to be forged is blocked and finished on one heat through the use of a die having both a block impression and a finish impression in the same die. This also covers the case where two tools mounted in the same machine are used, as in the case of aircraft pistons. Only one heat is involved for both operations.
BLOCK, FIRST AND SECOND - Blocking operation performed in a die having two blocking cavities in the same die; the part being forged is successively blocked in each impression all in one heat. As many as three blocker dies are sometimes needed for some forgings and up to three operations are sometimes required in each die.
BLOCK, FIRST, SECOND AND FINISH - The forging operation in which the part to be forged is passed in progressive order through three tools mounted in one forging machine; only one heat is involved for all three operations
BLOCKER IMPRESSION - The forging die impression which gives the forging its general shape, but omits any details that might restrict the metal flow; corners are well rounded. The primary purpose of the blocker is to enable the forming of shapes too complex to be finished after the preliminary operations; it also reduces die wear in the finishing impression.
BLOCKER-TYPE FORGING - A forging that approximates the general shape of the final part with relatively generous finish allowance and radii. Such forgings are sometimes specified to reduce die cost where only a small number of forgings are desired and the cost of machining each part to it final shape is exorbitant.
BLOOM - A semi-finished product of square, rectangular, or even round cross section, hot rolled, or forged. For steel, the width of a bloom is not more than twice the thickness, and the cross sectional area is usually not less than about 36 sq.in. No invariable rule prevails for distinguishing between blooms and billets; the terms are frequently used interchangeably.
BLOW - A particular forming operation or a give die or tool station.
BLOW-OUT (Fastener) - A defective condition which occurs on cold formed or headed nuts at the piercing operation. Visible indication of blow out is missing material at the piercing punch exit side.
BLUE ANNEALING - Heating hot-rolled sheet in an open furnace to a temperature with the transformation range and then cooling in air to soften the metal. The formation of a bluish oxide on the surface is incidental.
BLUE POLYMER - Polymer is a barrier coating because it creates a seal around the fastener which resists corrosion and abrasion. A phosphate-zinc base is initially applied to the fastener, followed by the polymer which bonds to the sub-coating. Commonly used to coast and identify concrete screws.
BLUING - The formation of a very thin blue oxide film on steel either by heating in air or by immersion in concentrated oxidizing solutions.
BLUNT START - The removal of the partial thread at the entering end of the thread.
BOARD HAMMER - A type of gravity drop hammer where wood boards attached to the ram are raised vertically be action on contrarotating rolls, then released. Energy for forging is obtained by the mass and velocity of the freely falling ram and the attached upper die. Also see Drop Hammer
BODY - The unthreaded portion of the shank of a threaded fastener. In blind fasteners, the portion of the rivet that expands into the parent material.
BODY - The portion of a breakstem blind rivet fastener that expands into the parent material.
BODY DIAMETER - The diameter of the body or smooth part of the bolt/screw above the threads. Also called shank diameter.
BODY LENGTH - See Shank Length
BODY-CENTERED CUBIC STRUCTURE (BCC) - A common crystal structure of steel. Refers to the arrangement of atoms within the metal. Atomically, it contains one lattice point in the center of the unite cell and eight corner points creating 2 full atoms per unit cell.
BOLSTER PLATE - A plate to which dies can be fastened; the assembly is secured to the top surface of a press bed. In press forging, such a plate may also be attached to the ram.
BOLT - An externally threaded fastener which accepts a nut in the application to produce the clamping load.
BOLT - A bolt is the term used for a threaded fastener, with a head, designed to be used in conjunction with a nut.
BOLT BLANK - A headed rod or bar intended for a subsequent threading operation.
BOLT CREEP/YIELD - Stress relaxation between the bolt and the washer is sometimes referred to as "bolt creep" or "bolt yield". This condition is the loss in bolt load due to elevated temperatures. The amount of loss depends on the bolt material, operating temperature, and the length of time at that temperature.
BOLT GRIP - For fasteners with a flat bearing surface head, the dimension from the bearing surface under the head to the end of the full diameter body, measured parallel to the axis of the fastener. For fasteners with a conical bearing surface head, the dimensions from the top of the head to the end of the full diameter, measured parallel to the axis of the fastener. Note that these definitions are similar to what some fastener standards use as the definitions for GRIP.
BOLT STOP - A spring loaded stop used in the trim station of Boltmakers that discharge trimmed bolts up through the heading side to the pointer. The stop keeps the trimmed bolts from falling back through the trim discharge tube and trim die.
BOND STRENGTH - The mechanical or chemical bonding capacity of an adhesive to both the insert and the base material.
BOROZING (BODDING) - A surface treatment procedure in which boron atoms are diffused into the workpiece by thermochemical treatment for purpose of increased hardness, wear and corrosion resistance.
BOSS - Protuberance on a plastic part designed to add strength and/or facilitate fastening or alignment.
BOSS - A relatively short protrusion or projection on the surface of a forging, often cylindrical in shape.
BOSS - A raised portion of material.
BOTTLING - The forward extrusion of a hollow part without a mandrel supporting the inside of the hole during extrusion.
BOTTOM DISCHARGE TRIM - A term used to describe the trim in the last station of a FORMAX., FORMAX PLUS, or large FORMAX PLUS machine.
BOUND BODY - (body-bound or fitted) A body which has a definite interference or extremely small clearance with mating hole.
BOW - The longitudinal curvature of the part of cutoff.
BOW DISTORTION - Out of flatness condition in sheet material commonly known as 'Oil Canning' in which, with the edges of the sheet restrained, the center of the sheet can be popped back and forth but cannot be flattened without specialized equipment.
BOW or CAMBER - The amount that a side of a fastener surface deviates from being straight.
BRAKE - A friction-operated mechanism used to arrest the movement of a press, feed, or other fabricated process or tool.
BRASS - An alloy composed primarily of two-thirds copper and secondarily one-third of zinc. Brass fasteners are non-magnetic and soft in comparison to steel. Brass has good strength and toughness, high electrical conductivity and an attractive lustrous finish. Brass is commonly used by the electrical and communications industries, builders hardware and some marine applications. Brass has good corrosion resistance, but not in salt water.
BRASS, ELECTROPLATED, LACQUERED - Brass electroplated which is then lacquered. Recommended for indoor decorative use only.
BREAK STEM - A fastener, which is installed by gripping and pulling the end of the mandrel/stem. As installation is completed, the end of the stem fractures at the braker groove and is discarded, leaving the head of the stem in the fastener body.
BREAKAWAY HEAD - The Breakaway head (also known as Breakoff or shear fastener) is a high-security fastener whose head breaks off during installation, during or immediately after the driving process, to leave only a smooth surface.
BREAKAWAY TORQUE - The torque necessary to put into reverse rotation a bolt that has not been tightened. Also known as Off-Torque" or "Removal Torque". Torque required to begin relative rotation between the part and mating thread absent an axial load. Subject to change with usage cycling. Considered the critical performance characteristic of a self-locking component.
BREAKDOWN - (1) An initial rolling or drawing operation, or a series of such operations, for reducing an ingot or extruded shape to desired size before the finish reduction. (2) A preliminary press-forging operation.
BREAKER GROOVE - A weakened groove in the stem or pin of a fastener allowing breakage at a pre-determined load.
BREAKLOOSE TORQUE - The torque required to effect reverse rotation when a pre-stressed threaded assembly is loosened.
BREAKLOOSE TORQUE - The torque required to effect reverse rotation when a pre-stressed threaded assembly is loosened. The amount of torque required to overcome the axial load of a seated fastener (pre-load), relieving the tension, initiating movement in the off direction. A value unrelated to prevailing torque.
BREAKOUT - Fractured portion of the cross section of a cut edge of stock. A condition naturally occurring during shearing, blanking, punching and other cutting operations.
BRIGHT DIPPING - Brief immersion in a solution used to produce a bright surface on a metal.
BRIGHT FINISH - A finish with a uniform non-directional smooth surface of high specular reflectance.
BRIGHT NICKEL - Electroplated silver-color finish. Used for appliances, hardware, etc.
BRIGHT PLATING (ELECTROLYTIC) - A process that produces an electrodeposit having a high degree of specular reflectance in a as-plated condition.
BRIGHT PLATING RANGE - The range of current densities within an electroplating solution produces a bright deposit und a given set of operating conditions. Brightener: An addition agent in an electroplating solution that improves the brightness of an electrodeposit.
BRINELL HARDNESS - The hardness of a metal or part, as represented by the number obtained from the ratio between the load applied on and the spherical area of the impression made by a steel ball forced into the surface of the material tested. The Brinell Hardness Number (BHN) is determined by measuring the diameter of the impression using a low power microscope, then matching this diameter with the load on a standard table.
BRINELL HARDNESS SCALE - A hardness scale which measures the indentation resistance of a metal. Brinell hardness testing is performed by forcing a steel ball onto a material and measuring the dimensions of the indentation left by the ball. Brinelling refers to surface fatigue caused by repeated impact or overloading. It is common cause of roller bearing failures, and loss of preload in bolted joints when a hardened washer is not used. Engineers will use the Brinell hardness of materials in their calculations to avoid this mode of failure. Fretting corrosion can cause a similar-looking kind of damage and is called false brinelling since the mechanism is different. It was the first widely used and standardized hardness test in engineering.
BRINELL HARDNESS TEST - A method of determining the hardness of metallic materials by applying a known load to the surface of the materials through a hardened steel ball of known diameter. The diameter (or depth) of the resulting impression in the metal is measured. The Brinell hardness number is taken as the quotient of the applied load divided by the area of the surface impression, which is assumed to be spherical.
BRINELLING - Permanent surface deformation of one component by another, resulting from compressive loading.
BRISTOL DRIVE - Bristol drive (or Bristol Spline) with four or six splines, but is not necessarily tamper-resistant. The grooves in the wrench are cut by a square-cornered broach, giving a slight undercut to the outer corners of the driver. The main advantage to this drive system is that almost all of the turning force is applied at right angles to the fastener spline face, which reduces the possibility of stripping the fastener.
BRITISH STANDARD BRASS - A specialist thread form based upon the Whitworth thread and consisting of 26 threads per inch whatever the thread diameter.
BROACH - Similar to trimming but removes a very small amount of metal for a more accurately finished part.
BROACH - The action of pulling the mandrel though the Avdel speed fastener in order to place it.
BROACH LOAD - The force required to pull the mandrel through the Avdel speed fastener in order to place it.
BROACHING - The process of removing metal by pushing or pulling a cutting tool, called a broach, along the surface.
BRONZE, ELECTROPLATED, LACQUERED - Has color similar to 80% copper, 20% zinc alloy. Electroplated and then lacquered. Recommended for indoor decorative use only.
BRUSH PLATING - As method of electrodeposition in which the electrolyte is applied with a pad or brush in contact with an electrode. The brush or pad is applied to the part to be processed which is given opposite polarity.
BSF - British Standard Fine. A thread form based upon the British Standard Whitworth form but with a finer thread (more threads per inch for a given diameter). This thread form was first introduced in 1908, the thread form is specified as BS 84:1956.
BSF BRITISH STANDARD FINE - A thread form based upon the British Standard Whitworth form but with a finer thread (more threads per inch for a given diameter). The thread form is specified in BS 84:1956.
BSW BRITISH STANDARD WHITWORTH - A thread form developed by Sir Joseph Whitworth in 1841. The thread form has rounded roots and crests, the thread form is specified as BS 84: 1956. This thread from was superceded by the United thread in 1948 and then the metric thread form.
BUCK-TAIL - The end of a solid tubular rivet, opposite the head, which is upset, or bucked (deformed) to expand the shaft diameter 1.5 times holding the rivet in place.
BUCKING BAR - A uniquely shaped weight used as an impact reaction mass, at the end of a fastener opposite to the applied load, in forming an upset button on a rivet
BUCKLING - A bulge, bend, kink, or other wavy condition of the workpiece caused by compressive stresses.
BUCKLING - Uncontrolled bending of stock during upsetting. Also encountered on tooling components without proper guide or exceeding the unsupported length.
BUCKLING - The tendency of a compression spring to bow or to deflect laterally, when loaded
BUFFER - A substance that, when contained in a solution counteracts changes in pH. Each buffer has a characteristic range of pH over which it is effective.
BUFFING (MOPPING) - The smoothing of a surface by means of a rotating flexible wheel to the surface of which is fine, abrasive particles are applied in liquid suspension, paste or grease stick form.
BUGLE HEAD - Similar to countersunk head with a smooth progression from the shank to the angle of the head, similar to the bell of a bugle. Bugle heads that allows the screw to depress the wood surface without breaking it. Used on Deck Screws and Drywall Screws.
BULBING - The physical action of the fastener body swelling (expanding radially) against the rear face of the joint when placed. Generally found in break stem fasteners and threaded inserts.
BULL NOSE - A style of bit where the tip of the bit is a larger diameter than the hex shank body.
BULLNOSE - To make a portion of a tool or die case that is not contained by the tool holder or die block larger in diameter. This gives improved support to the inserted assembly.
BUMP THREAD - A modified thread profile patented and trademark of Bosco Tool Inc. The thread form has a small projection at the pitch diameter that eliminates the clearance from the thread assembly on both flanks. By doing this it is claimed that resistance to vibration loosening is significantly improved.
BURN MARK - Heat discoloration created in the contact area of a welding electrode.
BURNING - Permanently damaging a metal or alloy by heating so as to cause either incipient melting or intergranular oxidation.
BURNISH - A forming operation that produces a smooth, polished surface by rubbing. Usually forcing a slightly larger diameter punch or pin through a hole in the part or forcing a part through a slightly smaller die orifice. The punch or die has a smooth surface to produce a polished finish.
BURNISHING - The process of producing a smooth surface by rubbing or rolling a tool against the surface.
BURNISHING - The smoothing of surfaces by ribbing under pressure, essentially without removal of the surface layer.
BURNT DEPOSIT - A rough unsatisfactory deposit produced by an excessive current density.
BURR - A small amount of material extended out from the edge of a hole, shoulder, etc. as the result of a machining operation.
BURR - Raised, sharp edge inherent in cutting operations such as shearing, blanking, punching and drilling.
BURR - A thin ridge or roughness left on forgings by cutting operation such as slitting, shearing, trimming, blanking or sawing.
BURR DIRECTION - Side of the stock on which burrs appear.
BURR FREE - In the context of a self-locking components, this reference applies to the milled area of strip and pellet installation areas.
BURR HEIGHT - Height of which burr is raised beyond the surface of the material.
BURR ROLLOVER - Condition of burr displacement resulting from mechanical deburring operation.
BURR-FREE - Edge without sharp protrusions
BURST - A seam or other wire defect which opens when the material is upset.
BUS BAR - A rigid conductor for carrying current, for example, to the anode and cathode bars.
BUSTER (PREBLOCKING IMPRESSION) - A type of die impression sometimes used to combine preliminary forging operations such as edging and fullering with the blocking operation to eliminated blows.
BUSTER (ROUGHER) - An impression employed in a die when considerable metal movement is required and which precedes a blocker cavity and a finisher cavity. Also known as breakdown/pancake, scalebreak, cheese.
BUTTON HEAD - A head with a low, rounded top surface and a flat bearing surface. Notably, a Button Head Socket Head Cap Screws.
BUTTON UPSET - Typically refers to the head preform of a bolt blank prior to the trimming operation.
BUTTRESS THREAD - A thread with an asymmetrical ridge that has one straight and one angled flank.
-
Glossary C.
C - National Coarse thread, or when followed by a number (ex: C-35) hardness measured on the Rockwell C Scale.
C-RING - A retention method used in bit holders that has a ring which locks around corresponding grooves in an insert bit to firmly hold it is place.
CADMIUM - An element that has atomic number 48. It is often used as a plating metal because it possesses superior corrosion resistance (compared to zinc) and high lubricity which lowers the frictional coefficient of the surface. Highly toxic; restricted under the RoHS directive.
CADMIUM ELECTROPLATING - Coating of threaded fasteners with cadmium can provide the parts with excellent corrosion resistance. The appearance of the coating is bright silver or yellow if subsequently passivated. The friction values associated with this coating are also comparatively low. A chromate conversion coasting is frequently applied to the surface to improve corrosion resistance. Cadmium is not frequently used because of the environmental and worker health problems associated with the coating process and should not be used in applications above 250 C or when contact with food is possible.
CADMIUM, ELECTROPLATED, (WAXED) - Bright silver-gray, dull gray, or black finish. Particularly effective corrosion protection, coloring and paint bonding. Good electrical conductivity quality. Not suggested unless absolutely necessary due to toxic content and extremely high cost.
CAGE CODE - The Commercial and Government Entity (CAGE) is a five-character ID number used extensively within the U.S. Federal government, assigned by the Department of Defense's Defense Logistics Agency (DLA). The CAGE code provides a standardized method of identifying a given facility at a specific location. CAGE code is also a part of a SAM registration.
CAM OUT - When a driver bit slips out of the drive recess of a fastener during installation once proper torque has been met. Repeated cam-out can lead to stripping of the drive. Most commonly occurs on Phillips drive fasteners.
CAMA - Concrete Anchor Manufacturer's Association
CAPACITY - The maximum rated amount of weight, force, or pressure that a stamping press or sliding tool can safely exert at the end of its stroke.
CAPTIVE SCREW - A captive screw is a specialist product that cannot be wholly removed from a hole once installed. There is a 'captive' area under the head, usually at or below the minor diameter of the threaded area at the end of the screw. They are available in a range of head styles, but the key similarity surrounds each product is that they all host a reduced thread.
CARBIDE PRECIPITATION - Carbon that breaks loose form its bond with the stainless solution when material is heated between 800-1400 degrees. Under severe corrosive conditions it can result in extra oxidation and surface corrosion.
CARBON POTENTIAL - A measure of the ability of an environment containing active carbon to alter or maintain, under prescribed conditions, the carbon content of the steel exposed to it. In any particular environment, the carbon level attained will depend on such factors as temperature, time and steel composition.
CARBON RANGE - In steel specifications, the carbon range is the difference between the minimum and maximum amount of carbon acceptable. Carbon adds strength to stainless steel ,but also lowers corrosion resistance. The more carbon there is, the more chromium must be added, because carbon offsets 17 times its own weight in chromium to form carbides, thus reducing the chromium available for resisting corrosion.
CARBON RESTORATION - Replacing the carbon lost in the surface layer from previous processing by carburizing this layer to substantially restore the original carbon level.
CARBON STEEL - Steel which owes its properties (up to 1.2% carbon) chiefly to various percentages of carbon and is without substantial trace amounts of other alloying elements. Higher percentages of silicon and manganese may be added for composition control.
CARBONITRIDING - A case-hardening process in which a suitable ferrous material is heated above lower transformation temperature in a gaseous atmosphere of such composition as to cause simultaneous absorption of carbon and nitrogen by the surface and, by diffusion create a concentration gradient. The process is completed by cooling at a rate that produces the desired properties in the workpiece.
CARBURIZING - Absorption and diffusion of carbon into solid ferrous alloys by heating, to a temperature usually above Ac3, in contact with a suitable carbonaceous material. A form of case hardening that produces a carbon gradient extending inward from the surface, enabling the surface layer to be hardened either by quenching directly from the carburizing temperature or by cooling to room temperature, then re-austenitizing and quenching.
CASE - (1) The surface layer of an iron based alloy which as been made substantially harder than the interior by some form of hardening. (2) The container or holder of the inserts on either the punch or die side of the tooling.
CASE - (1) The surface layer of an iron-base alloy that has been suitably altered in composition and can be made substantially harder that the interior or core by a process of case hardening: and (2) the hardened surface layer of a piece of steel that is large enough to have a distinctly softer core or center.
CASE HARDENED - Carburizing, nitriding or cyaniding and subsequent heat treating produces a case-hardened fastener, which is a fastener of ferrous material having a surface harder than the core.
CASE HARDENING - A generic term covering several processes application to steel that change the chemical composition of the surface layer by absorption of carbon, nitrogen, or a mixture of the two and by diffusion, create a concentration gradient. The processes commonly used are carburizing and quench hardening; cyaniding; nitriding; and carbonitriding. The use of the applicable specific process name is preferred.
CASSETTE - Also known as sub-bolster, die assembly, trim and pierce assembly. An assembly of top and bottom dies and/or tools of each forming station assembled into one unit.
CASSETTE - The individual punch holder or die holder on the large FORMAX Plus machines. A part of the tool changing system.
CAST (PROOF) - Any reproduction of a die cavity in any material, frequently lead, plaster or epoxy, used to confirm the exactness of the cavity. See Die Proof.
CAST-IN-PLACE ANCHOR - A headed bolt, stud or hooked bolt installed into formwork prior to placing concrete.
CASTELLATED - Having grooves or slots on its upper face.
CATASTROPHIC HAZARD - (1) A hazard that could result in a mishap causing fatal injury to personnel, and/or loss of one or more major elements of the flight vehicle or ground facility (2) A condition that may cause death or permanently disabling injury, major system or facility destruction on the ground, or loss of crew, major systems , or vehicle during the mission.
CATHODE - The material in a corrosive attack that attracts electrons from the anode.
CATHODE - In electrolysis, the electrode at which positive ions are discharged, negative ions are formed or other reducing reactions occur.
CATHODE EFFICIENCY - Current efficiency of a specified cathodic process.
CATHODE FILM - The think layer of solution which is in contact with the cathode and differs in composition from the bulk of a solution.
CATHODIC (DIRECT) CLEANING - Electrolytic cleaning in which the work piece is the cathode.
CATHODIC BARRIER PROTECTION - Method of fighting corrosion in which a plating metal is attached to the surface of a substrate material (e.g. fasteners). The plating metal is anodic to the substrate (thereby making the substrate cathodic) so that the plating metal will corrode first, thus protecting the substrate material. It is a method used to protect fasteners from galvanic corrosion.
CATION - A positively charged ion.
CAVITY, DIE - The machined recess in a die that gives the forging its shape.
CELLULAR MANUFACTURING - An approach in which manufacturing work centers (cells) have the total capability to produce an item or group of similar items.
CEMENTATION - The introduction of one or more elements into the outer portion of a metal object by means of diffusion at high temperature.
CEMENTATION - The process of introducing elements into the outer layer of metal objects by means of high-temperature diffusion.
CEMENTITE - This is a carbon rich steel also known as iron carbide (Fe3C). In carbon steel, it either forms from austenite while cooling or from martensite during tempering.
CENTER-LINE to EDGE DISTANCE - The minimum distance from the edge of a panel to the center of the mounting hole that a self-clinching fastener can be installed without causing a distortion or bulge in the panel.
CENTERING DISC - Used behind the punch holders on machines with punch rockers. It acts as a hardplate for the tooling and the centering block for the punch holders. Allows the punch holder to be removed from the punch rocker and re-installed back on center.
CENTRAL BURSTING - Also refers to the single internal burst that can occur at the junction of a head upset and the start of the shank.
CENTRIFUGAL CAPACITY(N) - A mathematical expression for determining the speed (in revolutions per minute, rpm) at which a retaining ring will lose cling on the groove.
CERTIFICATE OF COMPLIANCE (COC) - Certification stating that parts meet all required specifications it is being sold under.
CERTIFICATION - A procedure and action to verify in writing a process or material meets a set of applicable standards. This helps ensure consist products for both manufacturer and end users.
CETYL ALCOHOL - An organic, fatty alcohol applied to fasteners as a lubricant
CHAIN DIMENSIONING - Drafting practice which dimensions repetitive features from each other rather than a common datum
CHAMFER - (v) To bevel a sharp external edge. (n) A beveled edge.
CHAMFER - To break or remove sharp edges or corners of forging stock by means of straight angle tool or grinding wheel.
CHAMFER - The bevel on a corner that is at an angle to either side.
CHAMFER ANGLE - The angle of the chamfer measured from the normal to the axis of the fastener and generally specified in conjunction with either a length or a diameter.
CHAMFER POINT - A truncated cone point, the end of which is approximately flat and perpendicular to the fastener axis. Three points on threaded fasteners generally have point included angles of 45 to 90 degrees and a point diameter equal to or slightly less than minor diameter of the thread. This point is intended to facilitate entry of fasteners into holes at assembly.
CHARACTERISTIC DESIGN VALUE - The nominal strength for which there is 90% confidence that there is a 95% probability of the actual strength exceeding the nominal strength.
CHARPY IMPACT TEST - An impact test in which a specially V-notched specimen is broken by the impact of a falling pendulum. The energy absorbed in fracture is a measure of the impact strength or notch toughness of the sample.
CHARPY TEST - A test made to determine the notched toughness, or impact strength, or a material. The test gives the energy required to break a standard notched specimen supported at the two ends.
CHASING THREADS - Cutting screw threads by moving a tool along the axis of the work to be threaded.
CHECK - Crack in a die impression, generally due to forging pressure and/or excessive die temperature. Die blocks too hard for the depth of the die impression have a tendency to check or develop cracks in impression corners.
CHEESE HEAD - See Fillister Head
CHELATE COMPOUND - A compound in which the metal atom forms part of a ring-structure and is not readily ionized.
CHELATING AGENT - An organic compound capable of forming a chelate compound with a metal ion.
CHEMICAL ANALYSIS - Qualitative analysis consists of separating a substance into its component elements and identifying them, in quantitative analysis the proportion of all component elements are determined.
CHEMICAL POLISHING - Immersion in a solution to improve the surface smoothness of a metal. (Not to be confused with bright dipping.)
CHEVRON - An internal burst defect on a forward extruded part. Usually occurs in multiples along the length of the forward extrusion, and is caused by multiple extrusion passes over the same section of the part.
CHIP - An unwanted piece of metal that is removed from a workpiece. Chips are formed when a tool cuts or grinds metal.
CHISEL POINT - Typically a horizontal knife edge added to the end of a kickout pin. The purpose is to keep the part from rotating during the kickout or insertion of a part into or from a die. Required when the formed part must be oriented between forming operations, The kickout pin is also keyed to the tooling to keep it from rotating.
CHISEL POINT 45 DEGREE STUD - A full thread stud used to break the capsule of adhesives in an anchoring device to secure it in the base material.
CHOKE SLEEVE - A special kickout sleeve or punch sleeve with a restricted orifice to contain the slug after piercing.
CHOP - A die forging defect; metal sheared from a vertical surface and spread by the die over an adjoining horizontal surface.
CHROMATE - A secondary dipping process after plating increasing corrosion resistance, adding brilliance. It also can be colored. Standard clear chromate leave a bluish-white hue; other colors may be chosen, such as yellow, olive drab or black.
CHROMATING - Forming a conversion coating on a metal surface by means of a solution containing chromium compounds usually in the hexavalent form.
CHROME - A type of coating that provides corrosion resistance and aesthetically pleasing (or decorative) appearance.
CHROME - Chrome plating is applied in two methods. Hard-chrome deposits a thick layer of chrome to the fastener. This gives the part a very hard finish and superior wear resistance but does not offer much protection to corrosion. A nickel-chrome finish is achieved by applying a flash of chrome on top of nickel plating. This process offers resistance to tarnishing and corrosion.
CHROMIUM - Chromium, a blue-white metal is the most important element in providing corrosion resistance in stainless steel. By adding 12 percent chromium to ordinary steel, stainless steel is formed. Chromium offsets the corrosive effects of carbon found in steel and is the primary factor in the ability of the stainless to form a passive film on its surface providing corrosion resistance.
CHROMIUM, ELECTROPLATED - Bright blue-white, lustrous finish. Has relatively hard surface. Used for decorative purposes or to add wear resistance.
CHUCKING LUG - A lug or boss to the forging so that (on center) machining and forming can be performed with one setting or chucking; this lug is machined or cut away on the finished item.
CLAMP FORCE - The force between two components held together in a joint. Clamp force is typically imparted to a joint through threaded fasteners. Maintaining an appropriate amount of clamp force is critical to the functionality of any joint. Differs from preload in that preload is applied during assembly while clamp force may change after relaxation and elastic interactions have taken place.
CLAMP LOAD - The compression load induced in the joint by the installed fastener. The residual clamp load (or joint pre-tension) is the compressive load remaining in the joint after the fastener is installed. Higher clamp loads are experienced during fastener installation (pulling force).
CLAMP LOAD - Also called initial load or preload, is created when tension is applied on a bolt and results in equal force and measures of the compression of two parts. Typically measured in "pounds", a value of clamping force imparted by the elastic tension of the fastener in the assembled parts. It is commonly calculated as 75 percent of minimum proof load.
CLAMP MARKS - Slight indentations at the edge of one side of stock caused by pressure from turret press holding devices.
CLAMPING FORCE - The compressive force which a fastener exerts on the joint.
CLASS - Used in metric; class is a material designation equivalent to the US term Grade (ex. Class 10.9)
CLASS 1A/1B THREADS - These threads have a large tolerance and a wider allowance fit. A represents the external thread and B represents the internal thread.
CLASS 2/A/2B THREADS - The most common class of threads. They have a moderate tolerance that balances manufacturing costs and performance.
CLASS 3/A/3B THREADS - These threads are made to an extremely close tolerance and have no allowance. Used for higher-strength fasteners in safety-critical applications.
CLASS OF FIT - The Class of Fit is a measure of the degree of fit between mating internal and external threads. Three main Classes of Fit are defined for metric screw threads: FINE: This has a tolerance class 5H for internal threads and 4h for external threads. MEDIUM: This has a tolerance class of 6H for internal threads and 6g for external threads. COARSE: This has a tolerance class of 7H for internal threads and 8g for external threads. For Unified threads, a similar designation as for metric threads is used. The thread classes used are 1A, 2A, and 3A for external threads and 1B, 2B and 3B for internal threads.
CLASS OF FIT (Metric) - The Class of Fit is a measure of the degree of fit between mating internal and external threads. Three main Classes of Fit are defined for metric screw threads:
- FINE: This has a tolerance class of 5H for internal threads and 4h for external threads.
- MEDIUM: This has a tolerance class of 6H for internal threads and 6g for external threads.
- COARSE: This has a tolerance class of 7H for internal threads and 8g for external threads.
CLASS OF THREAD - Classes of threads are distinguished from each other by the amount of tolerance or tolerance and allowance specified. Classes 1A, 2A and 3A apply to external threads, and Classes 1B,2B and 3B apply to internal threads. Classes 2 and 3 apply to both external and internal threads. There is one other Class of thread, Class 5 Interference-fit for special applications.
CLEANING - The process of removing scale, oxides, or lubricant - acquired during heating for forging or heat treating - from the surface of the forging. See Blasting, Pickling, Tumbling.
CLEAR CHROMATE - Used on Zinc and Cadmium plated parts; very good to excellent corrosion resistance. Clear bright lustrous finish applied to zinc or cadmium plated surfaces for added corrosion protection.
CLEARANCE - An amount of space or distance between two objects.
CLEARANCE FIT - An internal and external thread design whose combination of allowances and tolerances allow for a free running assembly.
CLENCH - The ability of a fastener to draw together and hold together initially separated joint material components, during the installation process (i.e. 'gap closing' ability).
CLING - A value that signifies the amount of "interference fit" between a retaining ring and its groove.
CLIP MANUFACTURING - The act of utilizing various metal forming processes to create structural or decorative metal clips.
CLOCK SYSTEM - A system that identifies the strengths of nuts by dots or circle radius lines.
CLOSE ENDS - The end of the wire coil on a compression spring where it touches the next coil
CLOSE-TOLERANCE FORGING - One held to closer-than-conventional dimensional tolerance so that little or no machining is required after forging.
CLOSE-WOUND OR CLOSE-COILED - Coiled with adjacent coils touching
CLOSED & GROUND ENDS - (Also known as Squared & Ground) The ends of a compression spring where the pitch of the end coils is reduced to zero and the ends are ground square with the spring axis.
CLOSED & UNGROUND ENDS - (Also known as Closed and Square ends, or Squared Ends) The ends of a compression spring where the pitch of the end coils is reduced to zero.
CLOSED AND GROUND ENDS - Where the end of the wire coil touches the next coil and is ground flat as to sit flat on a compression spring.
CLOSED DIE FORGING - The shaping of hot metal completely within the walls of cavities of two dies that come together to enclose the workpiece on all sides. The impression for the forging can be entirely in either die or divided between the top and bottom dies. Impression-die forging, often used interchangeably with the term closed-die forging, refers to a closed-die operation in which the dies contain a provision for controlling the flow of excess material, or flash, that is generated. By contrast,, in flashless forging, the material is deformed in a cavity that allows little or no escape of excess material. See Impression Forging.
CLOSED END - (1) the term used in the blind threaded insert industry to describe an internal threaded insert with metal enclosing the end of the thread opposite the head. (2) In self-clinching fastener industry this style of part is said to be blind or have blind thread. Closed end parts are used to prevent long screws from interfering with other components or for protecting the mating threads from corrosive environments.
CLOSING-IN - The forging operation that locally reduces diameters in hollow forgings.
CLOSURE, DIE - A term frequently used to mean variations in thickness of a forging.
CLUTCH DRIVE RECESS - There are two types of Clutch screw drives. Type A and Type G. Type A is known as the "Standard Clutch", resembles a bow tie , with a small circular "knot" at the center. Popular in the 1940 & 50a with GM cars and trucks and buses. Type G resembles a butterfly, and lacks the center "knot". This type of screw head is commonly used in the manufacture of mobile homes and RVs. The clutch head was designed to be driven with a flat-blade screwdriver as well as a clutch driver.
CLUTCH RECESS - Non-tapered recess gives skid proof straight driving without cam-out. Uses a clutch driver.
CNC MACHINING - Computer Numerical Control machining uses computers to control and monitor the movements of a machine tool during the manufacturing process.
CNF TRANSFER - An abbreviation for Cold Nut Former transfer. The transfer allows for the 180 degree rotation of parts between forming stations. With the addition of special units, the parts can be transferred straight across between stations as well. The fingers do not have cam controlled opening and closing so blanks are typically gripped on the maximum outside dimension and the forming punches passed through the fingers. Typically used for shot run nut type products.
COAP - An abbreviation for Change Over Assistance Package. This is a special die block and tool package for quick changeover. Removal of mechanical fasteners allow removal of the entire die block as a unit and the entire tool package as a unit.
COARSE THREAD - This thread type has a greater pitch and is more forgiving of thread nicks. Coarse threads have a greater resistance to thread stripping and are better for assemblies which encounter fatigue loading
COATING - The application of some material such as metal organic compound, etc. to the surface of a fastener. There are a variety of different types such as dip-spin, mechanical and hot dip galvanizing, powder coatings and spray-on coatings.
COEFFICIENT OF FRICTION - A dimensionless number representing the ratio of the friction force to normal force. Typically for threaded connections it is between 0.10 to 0.18 but can vary significantly depending upon the materials used and whether a lubricant has been used. In relation to threaded fasteners, the coefficient of friction can be further sub-divided into the coefficient of friction between the threads and the coefficient of friction under the nut face. There is in general a difference in values between the two coefficients due to typically the contact surfaces being different.
COEFFICIENT OF FRICTION - A dimensionless number representing the ratio of the friction force to normal force. Typically for threaded connections it is between 0.10 to 0.18 but can vary significantly depending upon the materials used and whether a lubricant has been used. In relation to threaded fasteners, the coefficient of friction can be further sub-divided into the coefficient of friction between the threads and the coefficient of friction under the nut face. There is in general a difference in values between the two coefficients due to typically the contact surfaces being different. For example, a zinc plated nut on a zinc plated bolts, the thread coefficient of friction would be due to zinc plating contacting zinc plating. The nut face coefficient of friction would be due to zinc plating contacting the joint surface finish.
COGGING - The reducing operation in which an ingot is worked into a billet by the use of a forging hammer or a forging press.
COIL FEEDING - A system where material is delivered to the stamping equipment from cylindrically wound sheets or strips.
COIN - To form to more exacting dimensions and shape by re-striking. The amount of forming is usually relatively small.
COIN- SLOT DRIVE - Coin-slot drives are so-called because of the curved bottom of the recess, which facilitates driving them with a suitable coin.
COINING - (1) A post-forging process-on hot or cold parts-used to attain closer tolerances or improved surfaces. (2) A closed-die squeezing operation in which all surfaces of a workpiece are confined or restrained, resulting in a well-defined imprint of the die on the work.
COINING DIES - Dies in which the coining or sizing operation is performed.
COLD FINISHING - Changing the shape of or reducing the cross section of steel while cold- usually accomplished by rolling, drawing through a die, or turning.
COLD FLOW - Continued deformation of a material under stress.
COLD FORGING - Various forging processes conducted at or near ambient temperatures to produce metal components to close tolerances and net shape. These include bending, cold drawing, cold heading, coining, extrusion (forward or backward), punching, thread rolling and others.
COLD FORMING - The shaping of a metal at room temperature.
COLD HEADING - Forcing metal to flow cold into dies to form thicker sections and more less intricate shapes. The operation is performed in specialized machines, where the metal , in the form of a wire or bar stock, may be upset or headed in certain sections to a larger size and, if desired, may be extruded on other sections to a smaller diameter that the stock wire. Cold heading causes an increase tensile strength and hardness and a decrease in ductility. AKA, Cold Form or Cold Working.
COLD HEADING - Plastically deforming metal at ambient temperatures to increase the cross-sectional area of the stock (either solid bar or tubing) at one or more points along the longitudinal axis See Heading and Upsetting.
COLD HEADING STOCK - Stock material produced under closely controlled manufacturing and inspection methods to be suitable for heading and to be free from those defects causing fractures during heading.
COLD LAP - A flaw that results when a workpiece fails to fill the die cavity during the first forging. A seam is formed as subsequent dies force metal over this gap to leave a seam on the workpiece surface. See cold shut.
COLD SAW - Mechanical sawing machine used to produce cut pieces prior to the forging operation. Sawing is carried out on the material at ambient temperature.
COLD SHUT - Also known as lap or fold. A defect such as lap that forms whenever metal folds over itself during forging. This can occur where vertical and horizontal surfaces intersect.
COLD SHUT - A fissure or lap on a formed surface which has been closed without fusion during the forming process; the surface folds over on itself.
COLD SWAGING PROCESS - A method of reducing or forming steel or other material while cold, by drawing to a point or reducing the diameter, as may be required.
COLD SWILL - Washing in cold water.
COLD TREATMENT - Exposing to suitable subzero temperatures for the purpose of obtaining desired conditions or properties, such as dimensional or microstructural stability. When the treatment involves the transformation of retained austenite, it is usually followed by a tempering treatment.
COLD TRIMMING - Removing flash or excess metal from the forging in a trimming press when the forging is at room temperature.
COLD WORK - To deform metal stock while the metal is at ordinary room temperature. Altering the geometry of a metal component below the recrystallization temperature by plastic deformation. Processes include rolling, drawing, pressing, spinning, extruding and cold heading.
COLD WORKING - Permanent plastic deformation of a metal at a temperature below its recrystallization point - low enough to produce strain hardening. Usually, but not necessarily, conducted at room temperature. Also referred to as cold forming or cold forging. Contrast with hot working.
COLD-COINED FORGING - A forging that has been restruck cold in order to hold closer face distance tolerances, sharpen corners or outlines, reduce section thickness, flatten some particular surface, or, in non-heat-treatable alloys, increase hard-ness.
COLLAR - A raised ring or flange of material on the head or shank of a fastener.
COLLAR - A fastening component that is attached to a pin to clamp one or more pieces together and provide a permanent installation. Method of attachment may be by threading, swaging, forming or other means.
COLLAR CROPPER/SPLITTER - An installation tool attachment that removes collars from lockbolt fasteners.
COLOR PHOSPHATE COATINGS - Chemically produced color coating. Available in blue, green, red, purple, and other colors.
COLOR, CHROMATE FINISH - Olive drab, blue (used often for metric fasteners), bronze, red and other colors. A secondary dipping process after plating increasing corrosion resistance.
COLOURING OFF - Light final buffing
COLUMBIUM - A metal which may be added to chrome-nickel stainless steel to improve its welding and general heat-resistant qualities, by preventing carbide precipitation.
COMBINATION DRIVES - Some screw drives have heads designed to accommodate more than one kind of driver, sometimes referred to as combo-head or combi-head. The most common of these are a combination of a slotted/Phillips head for furniture drawers and combined slotted/Pozidriv for electrical switchgear or nicknamed "electrician's screws". The idea is that the first screwdriver out of the toolbox is used and the user does not have to waste valuable time searching for the correct driver. Their rise to popular use has been in spite of the fact that the head is weaker and neither a flat screwdriver or Pozidriv/Phillips screwdriver as appropriate is fully successful in driving these screw to the required torque.
COMBINATION PUNCH HOLDER - A special tool holder on a machine with a punch rocker. It allows for either a stationary or sliding tool. Can be used in either the cone or finish blow.
COMMERCIAL FASTENER - A fastener manufactured to published standards and stocked by manufacturers or distributors. The material, dimensions, features, and finish of commercial fasteners conform to the quality level generally recognized by manufacturers and users as the commercial quality.
COMMINGLING - A term used to describe the undesirable practice of mixing fasteners from different batches that are the same size and grade in the ssame container.
COMPARATOR - A device for inspecting screw threads and outlines by comparing them with a greatly enlarged standard chart.
COMPLETE HOLE FILL - Fasteners with this feature will expand to fill irregular, slotted, oversized, or misaligned holes.
COMPLETE THREAD - The length of completed thread is the length of that cross section of a threaded length having full form at both crest and root. Where there is a chamfer at the start of the thread not exceeding two pitches in length, it is included within the length of the complete thread. The thread length on the drawing shall be the gaging length or the length of threads having full form, i.e. the partial threads shall be outside or beyond the length specified. When designing threaded products, it is necessary to take cognizance of : (1) Such permissible length of chamfer and (2) the first two threads which by virtue of HI-LO gaging practice may exceed the product limits and which may be included within the length of complete thread. However, where the application is such as to require a minimum or maximum number, or length, of complete threads, the specifications shall so state. Similar specification is required for definite length of engagement.
COMPLEXING AGENT - A compound that will combine with metallic ions to form complex ions.
COMPOSITE MATERIAL FASTENERS - Fasteners designed for use in sandwich panel, honeycomb panel or other composite materials.
COMPOUND DIE - Tool used to pierce, form and blank a part at the same time, with one stroke of the press.
COMPRESSION FASTENER - A fastener which resists forces which tend to compress it.
COMPRESSION LOAD - The load which tends to compress or shorten the member. The value for compression strength may depend upon the degree of distortion.
COMPRESSION SPRING - An open-coiled spring that offers resistance when compressed.
COMPRESSION SPRING - A spring whose dimension, in the direction of the applied force, reduces under the action of that force.
COMPRESSION STRENGTH - The max amount of stress a metal can withstand under compression without fracturing or becoming permanently deformed.
COMPUTER AIDED DESIGN (CAD) - CAD programs allow users to digitally design parts that are to be milled, 3D printed or rendered.
COMPUTER AIDED MACHING (CAM) - This is the software used to control machine tools during the manufacturing of work pieces.
CONCAVITY - A concave condition applicable to the width of any flat surface.
CONCEALED HEAD - A type of fastener which, when installed, is completely hidden when viewed from the reverse side. Installed into a blind hole.
CONCENTRIC THREAD™ - The concentric threads are most 2D shapes except a circle that is expanding in size and rotating on each layer. One of its models screws around a corner. Patent Issued
CONCENTRIC, CONCENTRICITY - Two surfaces of a fastener are concentric when they have a common center or axis. Concentricity is the term used to describe this condition.
CONCRETE BREAKOUT - Anchor failure from the deepest embedment of the anchor to the surface of the base material at an angle of about 35 degrees; referred to as the cone of concrete because the breakout will be triangular shaped or cone shaped.
CONCRETE COMPRESSIVE STRENGTH - The specified compressive load carrying capacity of concrete used in design, expressed in pounds per square inch (psi) or megapascals (MP)
CONCRETE SCREW - Tapcon® brand concrete screws that are made from carbon steel and the threads are hardened to allow them to tap base material such as concrete, brick or block. The threads are an alternating high/low design with diamond cut notches. Tapcons are plated with a Climaseal® coating for excellent rust resistance.
CONDITION A - Means that fasteners should be solution annealed
CONDITION B - Means strain hardened to meet certain minimum tensile requirements.
CONDITIONING HEAT TREATMENT - A preliminary heat treatment used to prepare a material for a desired reaction to a subsequent heat treatment. For the term to be meaningful, the treatment used must be specified.
CONE - (1) Typically the first preform upsetting operation with the top remaining the wire diameter but the base increasing in diameter creating a conical shaped section. (2) The term used to indicate the gathering of metal before forming.
CONE BLOW - The first blow struck in a single die 2 blow header. It gets its name from the shape of the first punch which is typically that of a frustum of a cone.
CONE POINT - A sharp conical point designed to perform perforating or aligning functions at assembly.
CONE PROOF LOAD - This is an axial applied force applied to a nut when it is seated on a cone shaped washer which has an included angle of 120 degrees. Failure in this test is usually due to the nut splitting. The intention of the test is to introduce a nut dilation operation which will assess the potential detrimental effects of surface discontinuities. This type of test is sometimes applied to nuts which are intended for high temperature service.
CONE PUNCH HOLDER - The tool holder for the first blow on a machine with a punch rocker
CONIC THREADS™ - The profiles of the mated conic threads are on the same plane perpendicular to their direction of travel. These are best suited for pipe threads. Patent Issued.
CONNECTION POINTS - The supporting points that connect the slide to the upper drivetrain of the stamping press.
CONSTANT PITCH - Threads which are designed for repeated assembly and disassembly. Regardless of the diameter, the pitch will always be the same for constant pitch threads. The most common version is the 8-thread series.
CONTACT PLATING - The deposition of a metal coating upon a basis metal, by immersing the latter in contact with another metal in a solution containing a compound of the metal to be deposited (Not to be confused with immersion plating)
CONTINUOS FLOW MANUFACTURING (CFM) - Descriptive of material moving one piece at a time, at a rate determined by the needs of the customer in a smooth and untierrupted sequence without WIP.
CONTINUOS-ON-DEMAD (CSD) - A mode of operation where the press is automatically run without interruption based on input from upstream or downstream processes. The press will run constantly until a signal is received to instruct it otherwise
CONTROL LENGTH - The linear amount of guide of a part in either a die or punch, It is used during the transfer finger analysis.
CONTROL METHODS - The control method should match the joint specifications and the quality assurance required. For most critical applications, microprocessor-based controllers can perform 100% inspection of the dynamic applied torque and collect statistical process-control data. Such methods can eliminate the need for secondary inspection processes.
CONTROLLED CLOSING FINGERS - Special transfer fingers with a stop to limit how far closed the fingers can go without a blank in the fingers. used when there are short cutoff blanks, short stepped parts, or where the fingers could be hit by the punch when the machine is cycled empty.
CONTROLLED COOLING - Cooling from an elevated temperature in a predetermined manner to avoid hardening, cracking, or excessive internal stresses, or to produce a desired microstructure.
CONVENTIONAL FORGING - A forging characterized by design complexity and tolerances that fall within the broad range of general forging practice.
CONVERSION COATING - A coating consisting of a compound of the surface metal produced by chemical or electrochemical treatment. Example: chromate films on zinc or cadmium or oxide films on steel. Note: (Anodizeu coatings on aluminum or magnesium while satisfying these definitions are not normally conversion coatings.)
COOLING CURVE - A curve showing the relation between time and temperature during the cooling of a material.
COOLING CURVE - A curve showing the relation between time and temperature during the cooling of a material.
COPPER - Metallic element having atomic number 29. Possesses good corrosion resistance and ductility. Copper is nonmagnetic, malleable and has excellent electrical and thermal conductivity. Comes in a variety of colors. Shortcomings include a low strength-to-weight ratio and a loss of strength at low temperatures. Brass and silicon bronze are composed mainly of copper and gain their strength from the addition of other metals such as silicon.
COPPER STEEL - When any minimum copper content is specified, the steel is classed as copper steel. The copper is added to enhance corrosion resistance of the steel.
COPPER, ELECTROPLATED - Used for nickel and chromium plate undercoat. Can be blackened and relieved to obtain antique, statuary and Venetian finishes.
CORE - (1) The interior portion of an iron-base alloy that after case hardening is substantially softer that the surface layer or case; and (2) the relatively soft central portion of certain hardened tool steels.
CORE BOLT - The externally threaded, central part of a blind fastener.
CORNER - Three surfaces meeting at one point
CORNER RADIUS - Outside Radius
CORROSION - Gradual chemical or electro-chemical attack on a metal by atmosphere, moisture, or other agents. The wearing away or alteration of a metal by an electro-chemical reaction or by a direct chemical attack within its envirnoment.
CORROSION CRACKING, STRESS - A condition where cracks are induced and propagated in a fastener under combined effects of stress and corrosive environments.
CORROSION RESISTANCE - This describes the ability of a fastener to resist corrosion under specified conditions.
CORROSION, CONCENTRATION-CELL - Corrosion that begins in small cracks and crevices when two or more areas of a metal surface are in contact with different concentrations of the same solution. It only needs one metal and one electrolyte.
CORROSION, ELECTROCHEMICAL - Occurs when an electrical current flow from the metal of higher potential toward the lower. Exclusive to metals. Examples include galvanic corrosion and pitting corrosion.
CORROSION, GALVANIC - Corrosion involving two dissimilar metals in the presence of an electrolyte. The more active (anodic) of the two metals sacrifices its ions to the less active, thereby causing breakdown in the active metal.
CORROSION, PITTING - Localized corrosion in which a small bubble of air gets trapped on the surface of the metal. This bubble deprives the metal's surface of fresh oxygen supply, causing that area to become anodic. The change in the reactivity of the metal causes the formation of small, sometimes deep, pits. Also called Cavitation Corrosion.
COUNTER BALANCE - A system that counteracts the mass of the slide, slide attachments, and drive members. The counterbalancing force - provided by pneumatic cylinders - helps to eliminate force reversal and shock loading at the end of the press stroke.
COUNTERBLOW FORGING - One made by equipment incorporating two opposed rams, which simultaneously strike repeated blows on the workpiece.
COUNTERBLOW FORGING EQUIPMENT - A category of forging equipment in which two opposed rams are activated simultaneously, striking repeated blows on the workpiece at a midway point. Action is vertical or horizontal.
COUNTERBORE - (v) To enlarge a hole to a given depth. (n) (1) The cylindrical enlargement of the end of a drilled or bored hole. (2) A cutting tool for counterboring, having a piloted end the size of the drilled hole.
COUNTERBORING - The process of enlarging for part of its depth a hole previously formed and providing a shoulder at the bottom of the enlarged hole. Special tools called counterbores are generally used for this operation.
COUNTERBORING - Machining or coining operation to generate a cylindrical flat-bottomed hole.
COUNTERSINKING - The process of beveling or flaring (typically 30 to 60 degrees) the end of a hole. Holes in which countersunk head type fasteners are to be used must be countersunk to provide a mating bearing surface.
COUNTERSINKING - Machining or coining operation to generate a conical angle on a hole.
COUNTERSUNK - An internal chamfer. Also refers to a head style that is reduced to a flat head so the screw or bolt can be placed flush in the material.
COUNTERSUNK HEAD - A head, the underside of which is beveled to fit a flaring hole, such as a flat head or an oval head. The bearing surface of other types of heads is generally perpendicular to the body axis.
COVERING POWER - The ability of an electroplating solution under a given set of conditions to deposit metal on the surfaces or recesses or deep holes. (To be distinguished from throwing power). Critical current density (in electroplating): current density above or below which new and sometimes undesirable reactions occur.
CPM - An event oriented, project planning technique meaning critical path method.
CRACK - A clean, crystalline fracture which passes through or across the grain boundaries without inclusion of foreign elements.
CREEP - Plastic deformation or flow of metals held for long periods of time at stresses lower than normal yield strength. Especially important if temperatures of stressing are near recrystallization temperature of the metal. Permanent deformation of the material is caused by time, temperature, and pressure.
CREEP - Creep is deformation with time when a part is subjected to constant stress. Metals creep can occur at elevated temperature however with gasket materials it can occur at normal ambient temperatures. Creep resistance is an important property of gasket materials. Gasket materials are designed to flow under stress to fill any irregularities in the flange surface. The amount of creep sustained tends to increase with temperature. However once the tightening is completed it is important that no further flow occurs since such deformation will lead to a reduction in bolt extension and subsequently the stress acting on the gasket. If this stress is reduced to below a certain minimum, which depends upon the type and construction of the gasket and the opening temperature, a high rate of leakage can be anticipated to occur.
CREEP - The change in length of a spring when subjected to a constant force.
CREEP RANGE - Range of tension and temperature in which a material starts to experience creep,
CREEP STRENGTH - The maximum stress which can be applied to steel at a specified temperature without causing more than a specified percentage increase in length in a specified time.
CRES - Corrosion resistant steel (usually refer to 18-8 or 316 stainless steel)
CREST - That surface of the thread which joins the flanks of the thread and is farthest from the cylinder or cone from which the thread projects. For external threads, the crest is at the major diameter. For internal threads, the crest is at the minor diameter.
CREST -TO- CREST - A term used to identify a Flat Wave Compression spring in a "Series" configuration, having a sinusoidal waveform. The wave contour in each 360 degree turn provides a peak to valley relationship that decreases spring rate proportionally to the number of turns.
CREST CLEARANCE - As in a thread assembly, the distance, measured perpendicular to the axis, between the crest of a thread and the root of its mating thread.
CREST TRUNCATION - The crest truncation of a thread is the distance measured perpendicular to the axis, between the sharp crest (or crest apex) and the cylinder or cone bounds the crest.
CREVICE CORROSION - Refers to joints and crevices in a fastener assembly where lack of oxygen caused by limited space of by surface grease prevents the passive film on stainless from forming.
CRIMP LOCKING FEATURE - A squeezed portion of an internally threaded fastener that is used to prevent a mating screw from backing out due to vibration.
CRIMPING - The process of joining two pieces of metal together by deforming one of them such that it clamps or grips the other.
CRITICAL EDGE DISTANCE - The required distance from an unsupported edge of concrete to meet the maximum holding values.
CRITICAL HAZARD - A condition that may cause severe injury or occupational illness, or major property damage to facilities systems, or flight hardware.
CRITICAL SPACING - The required distance between anchors to meet the maximum holding values.
CRITICAL TEMPERATURE RANGE - Synonymous with Transformation Range which is preferred.
CROSS DRILLED - A fastener having one or more holes on the head or shank at right angles to, and normally intersecting, the axis of the fastener.
CROSS FORGING - Preliminary working of forging stock in alternate planes, usually on flat dies, to develop mechanical properties, particularly in the center portions of heavy sections.
CROSS SLOT - General term used to describe the head impression for driving a screw. Varieties include flat blade, Phillips, etc.
CROSS SLOTTED - Multiple slots are decorative and provide functional driving surfaces for many product styles and types.
CROWFOOT NUTRUNNER TOOL - Crowfoot nutrunners use special tool geometries to access hard-to-reah applications where more conventional tools won't fit. Gear-driven heads provide high levels of torque control. Special head designs can solve most demanding assembly problems.
CROWN - A spherical protrusion at the top of a fastener head
CRUCIFORM DRIVES - A cross shape drive recess for example the Phillips Drive or Pozidriv Drive recess.
CRYOGENIC TREATMENT (Cold treatment) - Treatment carried out after quenching to transform retained austenite into martensite, involving cooling and holding at a temperature below ambient.
CRYPGENIC (COLD TREATMENT) - Treatment carried out after quenching to transform retained austenite into martensite, involving cooling and holding at a temperature below ambient.
CTP POINT® - CTP Point is designed to prevent cross threading.
CTQ TREE - A tool to translate initial customer requirements into numerical or quantified needs for a product service.
CUMULATIVE TOLERANCE - Progressive accumulation of tolerances resulting from multiple operations or assembly of multiple parts.
CUP POINT - A point in the form of a cone, commonly having an included angle of 90 degrees, with a conical depression in the end commonly having an included angle of 118 degrees. The contact area is a circular ridge which has considerable holding power with slight penetration; applied to set screw generally.
CURE TIME - The elapsed time required for an adhesive anchor to develop its ultimate carrying capacity.
CURLING - The process of forming the edges of sheet metal into a circular cross-section by bending it around a shell or tube.
CURRENT DENSITY - Current expressed in amperes per unit area.
CURRENT EFFICIENCY - The proportion, usually expressed as a percentage, of the current that is effective in carrying out a given process in accordance with Faraday's law.
CUSTOM ASSEMBLIES - Components put together based on a customer's unique specifications using standard or non-standard parts and techniques.
CUSTOM METAL STAMPING DIE - A stamping die specially created for the production of customized, non-standard metal parts and components.
CUSTOM METAL STAMPINGS - Non-standard metal parts or components produced to customer-specific requirements by the action of a press operation or series of operations.
CUT THREAD - A thread produced by removing material from the surface with a form cutting tool.
CUTOFF - A blank is cut of from a coil. The diameter and length of the cut-off relates to the product diameter, finished bolt length and head size. The raw material is carbon alloy steel meeting the requirements of SAE and ASTM specifications for Hex Head Cap Screws and Bolts. The raw material has been pickled, annealed and coated prior to the manufacturing process. Also see Blank
CUTTER - The moving tooling component of the cutoff mechanism. It most often contains a hardened insert to extend the life of the cutting edge.
CUTTING TOOL - A device made of hard, tough material that is used to remove metal by creating chips.
CVD - An abbreviation for Chemical Vapor Deposition. This process is used to add a wear resistant coating to some tooling components, Commonly referred to as HOT process.
CYANIDING - A process of case hardening of an iron-base alloy be the simultaneous absorption of carbon and nitrogen by heating in a cyanide salt. Cyaniding is usually followed by quenching to produce a hard case.
CYCLE TIME - The normal time to complete a product or service operation. This is not the same as Takt Time.
CYLINDER - A solid, three dimensional shape with circular ends and straight sides.
-
Glossary D.
DACROMET - A high performance surface coasting that can be applied to fasteners. The coating consists of passivated zinc flakes that are stoved onto the metal surface. The coating can be coloured and eliminates the risk of hydrogen embrittlement associated with electroplated metal DACROMET is a registered trademark of Metal Coating International, Inc. f Chardon, Ohio.
DACROTIZED - Dacrotized is a pollution free ceramic coating for screws used with treated lumber. Coating is comparable to the corrosion resistance of hot-dep galvanized fasteners. Plating can typically withstand a 500-hour salt spray test. There is no risk of hydrogen embrittlement with Dacrotized plating.
DATUMS - Theoretically exact planes, lines or points from which other features are located on design drawings.
DEAD COILS - The coils of a spring that do not affect the spring rate
DEBURR - To remove chips, burrs, or other imperfections through a secondary operation such as grinding.
DEBURR - To remove the sharp, knife-like edge from parts.
DEBURRING - The removal of burrs, sharp edges, or fins by mechanical, chemical, or electrochemical means.
DECARBURIZATION - The removal of carbon from the surface of steel as a result of heating in a medium that reacts with the carbon. Decarburization is usually present to a slight extent in steel forgings. Excessive decarburization can result in defective products.
DECARBURIZATION - The loss of carbon from the surface of an iron-base alloy as the result of heating in a medium that reacts with the carbon.
DECARBURIZED - A fastener has a decarburized surface when the carbon content of the surface is lower than the carbon content of the core. Loss of carbon from the surface layer of a carbon-containing alloy due to reaction with one or more chemical substances in a medium that contacts the surface.
DECOMPRESSION POINT - The point at which there is zero pressure at the joint interface as a result of forces applied to the joint. If the applied force is increased beyond the decompression point, a gap will form at the interface. Analytically, a criteria of joint failure is often taken as when the applied force on the joint reaches the decompression point. This is because forces acting on the bolt(s) can dramatically increase at this point. Loading beyond this point can also result in fretting at the interface that will lead to bolt tension loss that will subsequently lower the decompression point. This process can continue until bolt failure does occur. The failure can be fatigue or other mechanism but the underlying cause was loading of the joint beyond the decompression point. It is for this reason that it is frequently taken as a failure criteria in analysis work.
DEDICATED TOOLING - Commonly referred to as (hard tooling) - is tooling made to produce a specific part.
DEEP DRAWING - The process of working metal blanks in dies on a press into shapes which are usually more or less cup like in character.
DEFECT - A defect is any deviation of a unit of product from the requirements of the specifications or standards to which it should be produced. Defects are classified as follows:
- Dud: A dud is an incomplete, mutilated, or foreign part.
- Major Characteristics: A major characteristic is one that could result in failure or materially reduce the usability of the product for its design capability as defined by the application standards and specifications.
- Minor Characteristics A: A minor characteristic A is one that does not materially reduce the usability of the product; and is of a lessor importance than those of established as Major.
- Minor Characteristics B: A minor characteristic B is one that has no great importance to the usability of the product, but one for which standards have been established. Normally the greatest possible latitude in acceptability is given Minor B defects.
DEFLECTION - The degree to which a washer is displaced under load. Belleville Spring washers are designed to produce predictable load versus deflection characteristics. Spring washers can be configured in parallel stacks to increase load or stack in series to increase deflection. The load and deflection can also be adjusted by adding or removing additional washers and/or by changing the sequence in which they are arranged.
DEFLECTION(S) - Relative displacement of the ends of a spring under the application of a force.
DEFORMA - A finite element analysis program for the cold forming process. This is the registered trademark of Scientific Technologies Corporation.
DELONIZATION (DEMINERALIZATION) - The removal of ions from a solution by ion exchange.
DEOXIDIATION - Process of reducing the oxygen content from steel during steel making process by adding strong oxide forming elements, such as aluminum.
DEOXIDIZER - Any item which removes or reduces the amount of oxygen in a part.
DEPOLARIZATION - A decrease in the polarization of an electrode.
DEPTH - The length of the space measured from the base of the root to an imaginary line spanning the crests of a thread
DEPTH OF CUT - Denotes how much material is being removed from a work piece with each pass of the tool.
DESCALING - The process of removing the flaky oxide film known as scale that forms on the surface of the fastener during production. Wire brushes, water spray, scraping equipment, and light blows to the metal are often used.
DESIGN FORM OF THREAD - The design form of an internal or external thread is the thread form in it's maximum metal condition. it is the same as the basic thread profile except that the thread roots are rounded. If either the internal or external thread form exceeds the design form of the thread profile then a potential interference exists.
DESIGN LOAD - The calculated maximum load that is to be applied to the anchor for the life of the structure. This should also be used for fasteners.
DESIGN SEPARATION LOAD - The limit tensile load multiplied by a separation factor of safety.
DESIGN SIZE - The size from which the limits of size are derived by the application of tolerances. When there is no allowance the design size is the same as the basic design.
DESIGN STRENGTH - The nominal strength of an anchor calculated per ACI 318, ICC-ES AC193 or ICC-ES AC308 and then multiplied by a strength reduction factor.
DESTRUCTIVE TEST - A test to determine the mechanical properties of a material or the behavior of an item which results in the destruction of the sample or item.
DETERGENT - A surface-active agent that possesses the ability to assist in cleaning soiled surfaces.
DETRIMENTAL YIELDING - Yielding that adversely affects fit, form, function, or integrity of the structure.
DFSS - An acronym meaning design for six sigma.
DFX - An acronym meaning design for X, where X represents an attribute such as service, assembly or manufacture.
DIAMOND PYRAMID HARDNESS TEST - An indentation hardness test employing a diamond pyramid indenter and variable loads enabling the use of hardness scale for all ranges of hardness from soft lead to tungsten carbide.
DIAMOND TIP BIT - The diamond grit is embedded in the steel substance and improves screw engagement reducing the risk of damage to the screw recess. This extra hard diamond coating wears less and grips better than a Titanium coating.
DIAPHRAGM (IN ELECTROPLATING) - A porous separator dividing anode and cathode compartments of an electroplating tank from each other or from an intermediate compartment.
DICHROMATE - In the early days of the plating industry, sodium dichromate, a solid, was used in the manufacture of the yellow chromate conversion coating baths. In modern times, no dichromate is used by platers, but the term "dichromate" is still widely used to describe the yellow zinc plating process. All chromate conversion coatings are true chromates and do not contain dichromate.
DICHROMATE - A secondary dipping in various colors such as yellow, brown, green or iridescent after plating increasing corrosion resistance and color finish.
DIE - (1) One of a pair of hardened metal blocks for forming, impressing, or cutting out a desired shape. (2) A tool for cutting external threads. Opposite of tap.
DIE - Tool with a void or cavity which is precisely fitted to a (PUNCH) used to shear or form sheet metal parts.
DIE - An individual tooling component with a forging cavity or the assembly of a case, inserts, fillers, etc. on the stationary side of the tooling
DIE BLOCK - The holder for the stationary side tooling. Can hold from one to six dies depending on the machine type. Metal blocks with impressions of the desired shape of a metal used during the open and closed-die forging.
DIE CASTING - A very accurate and smooth casting made by pouring a molten alloy usually under pressure into metal mold or die. Zinc Die Casted Fasteners.
DIE CHASER - The separate cutting tools used in die heads which actually cut the screw threads.
DIE CLEARANCE - Amount of space between the punch and die opening.
DIE CUSHION - An accessory that provides an opposing motion or counterforce to aid in the forming and release of the workpiece. Die cushions are typically pneumatic, but they may also be comprised of hydraulic systems, rubber, and springs. They may also be used for several operations including blank holding, uniform pressure regulations, knockout, et.
DIE HEIGHT - The distance measured from the bottom face of the ram or slide to the top of the bolster when the slide is positioned at the bottom of its stroke (bottom dead center/BDC).
DIE HOLDER - Also known as bolster, insert holder, can. Used to locate, clamp and support dies, die assemblies or die inserts.
DIE IMPRESSION - The portion of the die surface that shapes the forging.
DIE LIFE - The duration of a die impression or die block measured by how many forgings it has produced before it becomes too worn to use.
DIE LUBRICANT - A material sprayed, swabbed, or otherwise applied during forging to reduce friction and/or provide thermal insulation between the workpiece and the dies. Lubricants also facilitate release of the part from the dies and provide thermal insulation.
DIE LUBRICATION - The recirculating liquid lubrication applied to the tooling or workpiece during the forming operations. It reduces friction, minimizes tooling wear, lubricates the tooling, and helps to carry away the heat generated by the cold forming process.
DIE MARKS - Scratches, scrub marks, indentations, galling or burnishing of sheet metal workpieces by tooling.
DIE MATCH - Also known as mismatch. The alignment of the upper (moving) and lower (stationary) impression in the die.
DIE POINT - One of the least expensive pointing operations applied at the time of heading. This operation provides an end chamfer starting with a diameter smaller than the root diameter of the thread. The minimum reduction of the point is approximately 10% below the maximum minor diameter with an included angle of 40 to 50 degrees
DIE POINT - A forward extrusion that is stopped on the end of a shank forming a chamfer. See POINTING.
DIE PROOF (CAST) - A casting of the die impression made to confirm the exactness of the impression.
DIE PROTECTION - A system of protective measures, including proximately sensors, used to monitor the operation of the tooling, reducing the risk of heavy impacts and crashes due to equipment malfunction.
DIE RATIO - The ratio between the outside diameter of the case and the inside diameter of the insert.
DIE RETAINER - This device is used to hold the die case assembly in the die block on FORMAX or FORMAX Plus machines.
DIE SET - The assembly of the upper and lower die shoes (punch and die holders), usually including the guide pins, guide pin bushings, and heel blocks. This assembly takes many forms, shapes, and sizes and is frequently purchased as a commercially available unit. Also, two (or, for a mechanical upsetter, three) machined dies used together during the production of a die forging.
DIE SHIFT - The condition that occurs after the dies have been set up in a forging unit in which a portion of the impression of one die is not in perfect alignment with the corresponding portion of the other die. This results in a mismatch in the forging, a condition that must be held with in the specified tolerance.
DIE SHOES - The upper and lower plates of castings that constitute a die set (punch and die holder). Also a plated or block upon which a die holder is mounted, functioning primarily as a base for the complete die assembly. This plate or block is bolted or clamped to the bolster plate or the face of the press ram.
DIE SIDE INSTALLATION - The installation of a fastener into the die side of a punched mounting hole in a panel. The die side of a hole usually exhibits blow out and is larger in size than the punch side of the hole.
DIE SINKING - The process of machining impressions in die blocks.
DIE SLIDE - The linear distance a sliding die must move to allow for the backward extrusion of a hole, piercing , or the upsetting of a preform.
DIE SPACE - A drawing or series of drawings showing the dimensions in the tooling area that must be used during the tooling design.
DIE STRAIGHTEN - A straightening operation performed in either a hammer or press using flat or cavity dies to remove undesired deformation and bring the forging with the straightness tolerance.
DIEPAK - The die side assembly of the Formapak on FORMAX & FORMAX Plus machines. It includes the die block and faceplate.
DIES (DIE BLOCKS) - The metal blocks into which forging impressions are machined and from which forgings are produced.
DIES, FORGING - Forms for the making of forgings; generally consist of a top and bottom die. The simplest will form a completed forging in a single impression; the most complex, made up of several die inserts, may have a numbers of impressions for the progressive working of complicated shapes. Forging dies are usually of blocks and the balance of the impression in the other block.
DIES, GRIPPER - Clamping or lateral dies used in a forging machine or mechanical upsetter.
DIFFERENTIAL THERMAL EXPANSION (DTE) - DTE is experienced when connecting materials expand or contract at different rates during a change in temperature and impact the performance of the joint integrity.
DIFFUSION - The moment of atoms on one material into the crystal lattice of an adjoining material
DIFFUSION TREATMENT - Process introduced by diffusion of any metal or non-metal into the surface layer.
DIGITIZER - Scans and maps the surface of a real object, producing a 3D computer model for CAD/CAM programs.
DILATOMETER - An instrument for measuring the linear expansion or contraction in a metal resulting from changes in such factors as temperature and allotropy.
DILATOMETER - An instrument for measuring the linear expansion or contraction in a metal resulting from changes in such factors as temperature and allotropy
DIMENSION - Numerical values expressed in units of measure that are indicated on a drawing along with lines, symbols, and notes to define the characteristics of a fastener.
DIMPLE - A conical or domed impression on the end of a formed part often used as a preform for a subsequent forming or extruding operation.
DIN - An abbreviation for Deutsches Institut fur Normung, the German standards body. In reference to fasteners DIN indicates fasteners that conform to the dimensional and mechanical properties of metric fasteners. Specific metric standards (will be followed by the standard number for example DIN 932).
DIPHASE CLEANING - Cleaning by means of a liquid system that consists of an organic solvent layer and an aqueous layer. Cleaning is effected both both solvent and emulsifying action.
DIRECTIONAL BENDING - Fracture marks left on the surface from a fastener failure (breakage).
DIRECTIONAL PROPERTIES - Properties whose magnitude varies depending on the relation of the test axis to a specific direction within the metal or alloy.
DISC (DISK) - Pancake shaped forging (flat with a round cross-section); e.g. a blank for gears, rings and flanged hubs. Abbreviation is D.
DISCONTINUITIES - Small or large disfigurations in a fastener such as pits, tool marks, voids, laps, folds etc. Minor discontinuities are typically allowed, major as defined by carious military specifications AN, MS, NAS and NASM.
DISCONTINUITIES - Includes cracks, laps, folds, cold shuts, and flow-through, as well as internal defects such as inclusion, segregation, and porosity; internal discontinuities can be detected and evaluated using ultrasonic testing equipment.
DISH - This ring dimension is the height difference in the ring cross section's axis of symmetry between O.D. and I.D.
DISPLACE - The movement of metal from one place to another, a combination of extruding and upsetting.
DISPLACER - The portion of a self-clinching fastener that moves or displaces, the panel material. Usually the head, lugs, or knurled portion of the fastener. It could be a cylinder, a knurl, or a hex.
DISTRIBUTOR BLOCK - The component of the press lubrication system used to dispense oil/grease to the relevant areas of the equipment.
DMAIC - The core problem solving methodology used by many lean six sigma companies. The term refers to the steps: define, measure, analyze, improve and control.
DOG POINT - A cylindrical extension, or pilot, of diameter smaller than the minor diameter of the thread, commonly equal to about D/2 in length, with a conical section between it and the thread; usually used as a pilot in assembling or as the end of a set screw projecting into a fairly deep hole or clot. On small screws the dog point is usually extending in length about two-thirds the diameter of the thread. Recommended for ease in starting to insure against stripping fine threaded products, and to increase efficiency along production lines.
DOMED HEAD - Type of fastener head having a rounded, or semispherical, upper surface. Common on some types of Plow Bolts.
DOUBLE EXPANSION ANCHOR - The double expansion anchor is made up of five parts: a cone shaped expander nut, a hollow cone, outer body and two spring bands. The spring bands hold all the anchor parts together into one preassembled single piece and are made from zinc-plated steel. The hollow cone and cone nut are the same except that the cone nut has internal threads and are made from Zamak material. The out body is tubular and made from die-cast zinc alloy Zamak.
DOUBLE FORGING - A forging designed to be cut apart and used as two separate pieces.
DOUBLE HEADER - A situation where two parts have been accidentally formed in a die.
DOUBLE HEX - Double Hex is a socket recess with two coaxial offset hex recesses; it can be driven by standard hex key tools.
DOUBLE PUNCH OUT - Refers to a hollow part that has been pierced, then upset forming a second slug, and pierced a second time.
DOUBLE SALT - Two salts tat crystallise together in stoichiometric proportions but give there actions of the ions of the constituent single salts in aqueous solution. Example: Rochelle Salt.
DOUBLE TEMPERING - A treatment in which quench-hardened steel is given two complete tempering cycles at substantially the same temperature for the purpose of ensuring completion of the tempering reaction and promoting stability of the resulting microstructure.
DOUBLE TRIM - (1) A forming sequence where the formed part is trimmed twice. Such as in the forming of a hex flange bolt. The hex is sheared out of a preform shape and the flange is formed in one operation and then the flange diameter is sheared to size in the next forming operation. (2) A trimming technique using two opposing trim dies to reduce the amount of burr below a trimmed surface.
DOUBLE UPSET - The forming of a second upset on a part on the opposite end from the first upset. Requires the use of a special opening segment tooling.
DOUBLE-SQUARE - The Double-Square drive is two squares superimposed at 45 degree rotation, forming an 8 pointed star. The design is similar to a square drive (Robertson), but can be engaged at more frequent angles by the driver bit.
DOUBLE-START THREAD - Having two ridges wrapped around the cylinder
DPMO - An acronym meaning defects per million opportunities.
DPQ - An acronym meaning defects per opportunity.
DPU - A term meaning defects per unit.
DRAFT - The necessary taper on the side of a forging to allow removal from the dies; also applies to the die impression. Commonly expressed in degrees as the draft angle. As applied to open die forging, draft is the amount of relative movement of the dies toward each other through the metal in one application of power.
DRAFT ANGLE - The angle of taper, expressed in degrees (usually 5 to 7 degrees), given to the sides of the forging and the side walls of the die impression.
DRAFTLESS FORGING - A forging with zero draft on vertical walls.
DRAG-IN - The liquid carried into a bath y the objects introduced therein.
DRAG-OUT - The liquid carried out of a bath by the objects removed from there.
DRAW BOLT - A special contoured bolt and sleeve combination used to clamp a punch in a tool holder. Also used to hold in either the cutter or quill on FORMAX, FORMAX Plus and Large FORMAX Plus machines.
DRAW DIE - A tooling component located in a wire drawer It slightly reduces the diameter of the incoming wire and helps to press lubricant onto the surface of the wire. Also see DRAWING & WIRE DRAWER.
DRAWING - Drawing may refer to the pulling of steel through a die, as in drawing wire, or deforming steel in dies on a press (deep drawing).
DRAWING - (1) Engineering document depicting a part or assembly. (2) In metal forming, the stretching or compressing of a sheet metal part into a die by a punch to create a 3-dimensional part.
DRAWING - (1) A forging operation in which the cross section of forging stock is reduced and the stock lengthened between flat or simple contour dies. (2) In heat treating, the same as tempering.
DRAWING - (1) A metal forming operation done on a cup type part. The part is pushed through series of progressively smaller diameter dies with an mandrel. The thickness of the wall is reduced resulting in a longer part. (2) The process used to reduce the diameter of the incoming wire by passing it through an insert before entering the machine. See DRAW Die.
DRAWING OUT - The forging operation in which the length of a metal mass (stock) is increased at the expense of its cross section; no upset is involved. The operation covers converting ingot to pressed bar using (V) , round or flat dies.
DRESSOUT - A condition where the dimensions of a part or forging are changed by local grinding or machining to remove one or more defects thereby causing a localized imperfection of a maximum depth. The depth is the dimension of the dressout.
DRIFTING - In forging, the operation of forming or enlarging a hole by use of a tapered punch.
DRILED SHANK - A fastener shank with a hole drilled through it for a pin (i.e. cotter pin) or safety wire.
DRILL - (v) To sink a hole with a drill, usually a twist drill. (n) A pointed cutting tool rotated under pressure.
DRILL FLUTES - Allow drilled material to exit the hole. Completely embedded flutes can no longer remove these chips, which contain approximately 80% of the heat created by drilling process. A buildup of this material can cause the point on a self-drilling screw to over heat and fail.
DRILLED HEAD - A fastener head with a hole drilled through it for a safety wire.
DRILLING - The process of forming holes by means of specialized cutting tools called drills.
DRIVE SCREW - The male threaded part in the nose of a threaded insert-installation tool, which engages the female thread of inserts.
DRIVE TORQUE - Maximum torque to install a screw prior to contact of the head of the fastener with surface of the test plate.
DRIVE TYPE - SET SCREWS - Most set screws use socket (either hex or fluted) drive or a slot drive. The type of drive affects the seating torque that can be attained because it determines how much torque can be transmitted to the screw. Less torque can be transmitted through a slot drive than a socket drive. Therefore, holding power of the slotted screw is about 45% less.
DRIVER ADAPTER - A torque sensor that connects to a computer interface. A driver adapter is a device that expands the range of the tool.
DRIVER HEAD - A head, on a bolt or screw, designed for driving the fastener by means of a tool other than a wrench, such as a screwdriver.
DROP FORGING - Forming metal, usually under impact, by compression within dies designed to produce the required shape.
DROP FORGING - A forging made in closed or impression dies under a drop or steam hammer.
DROP HAMMER - A term generally applied to forging hammers wherein energy for forging is provided by gravity, steam, or compressed air.
DROP OUT/REFEED - A cold forming technique used with difficult to form materials, The part is formed in several stations and then dropped from the machine, The partially formed part can then be annealed and coated or heated and the re-fed into the machine for finish forming operations, Requires many machine specials and secondary equipment.
DROP-IN ANCHOR - A post-installed mechanical anchor consisting of an internally-threaded steel shell and a tapered expander plug. The bottom end of the steel shell is slotted longitudinally into equal segments. The anchor is installed in a pre-drilled hole using a hammer and a hand-setting tool. The anchor is set when the tapered expander plug is driven toward the bottom end of the anchor such that the shoulder of the hand-setting tool makes contact with the top end of the anchor. A drop-in anchor may also be referred to as a displacement controlled expansion anchor.
DTI WASHER - Direct Tension Indicating Washer; aka Load Indicating Washer. A washer that has raised bumps which plastically deform to become flat under a specific tensile load.
DUAL TRANSFER - A special design transfer for large Cold Formers. With one transfer slide installed, it moves like a normal straight across transfer. With the combination slide installed, it moves similar to a FORMAXPLUS PMP Transfer. The fingers lift from the face of the dies, the slide moves to the delivery station, and the transfer delivers the part into the next die. This combination transfer slide also as the ability to rotate parts 180 degrees between forming stations, but with very limited finger opening.
DUCTILE ANCHOR SYSTEM - The behavior of an anchor system where a ductile steel insert governs the design over concrete breakout, pullout, and adhesive bond.
DUCTILITY - The ability to permit change of shape without fracture. In steel, ductility is usually measured be elongation and reduction of area as determined in a tensile test. The lower the ration of its specified minimum yield strength to its specified minimum tensile strength, the grater the fastener's ductility.
DUCTILITY - Ability of a material to be bent or otherwise formed without fracture.
DUCTILITY - The property of a metal that enables it to stretch before rupturing.
DUCTILITY - A material under tensile stress with an elongation of at least 14% and an area reduction of at least 30% prior to rupture.
DULL FINISH - A finish virtually lacking both diffuse and specular reflecance.
DULL NICKEL - Whitish cast can be obtained by mechanical surface plating or a special satin bath.
DUMMY (OR DUMMY CATHODE) - A cathode used for removal decomposition of impurities from electroplating solutions.
DUPLEX RIVET - A two-piece rivet designed for easy upsetting and hole filling properties.
DWELL - Portion of a press cycle during which the movement of a member is zero or at least insignificant. Usually refers to the interval between the completion of the forging stroke and the retraction of the ram.
DYE-PENETRANT TESTING - Inspection procedures for detecting surface irregularities using penetrating liquids containing dyes or fluorescent substances.
DYEING (IN ELECTROPLATING) - Imparting a colour by the use of organic dyestuffs.
DYNAMIC FRICTION - Resistance to relative movement of two bodies that are already in motion.
DYNAMIC FRICTION - Resistance to relative movement of two bodies that are already in motion.
DYNAMIC LOAD - A load whose magnitude varies with time.
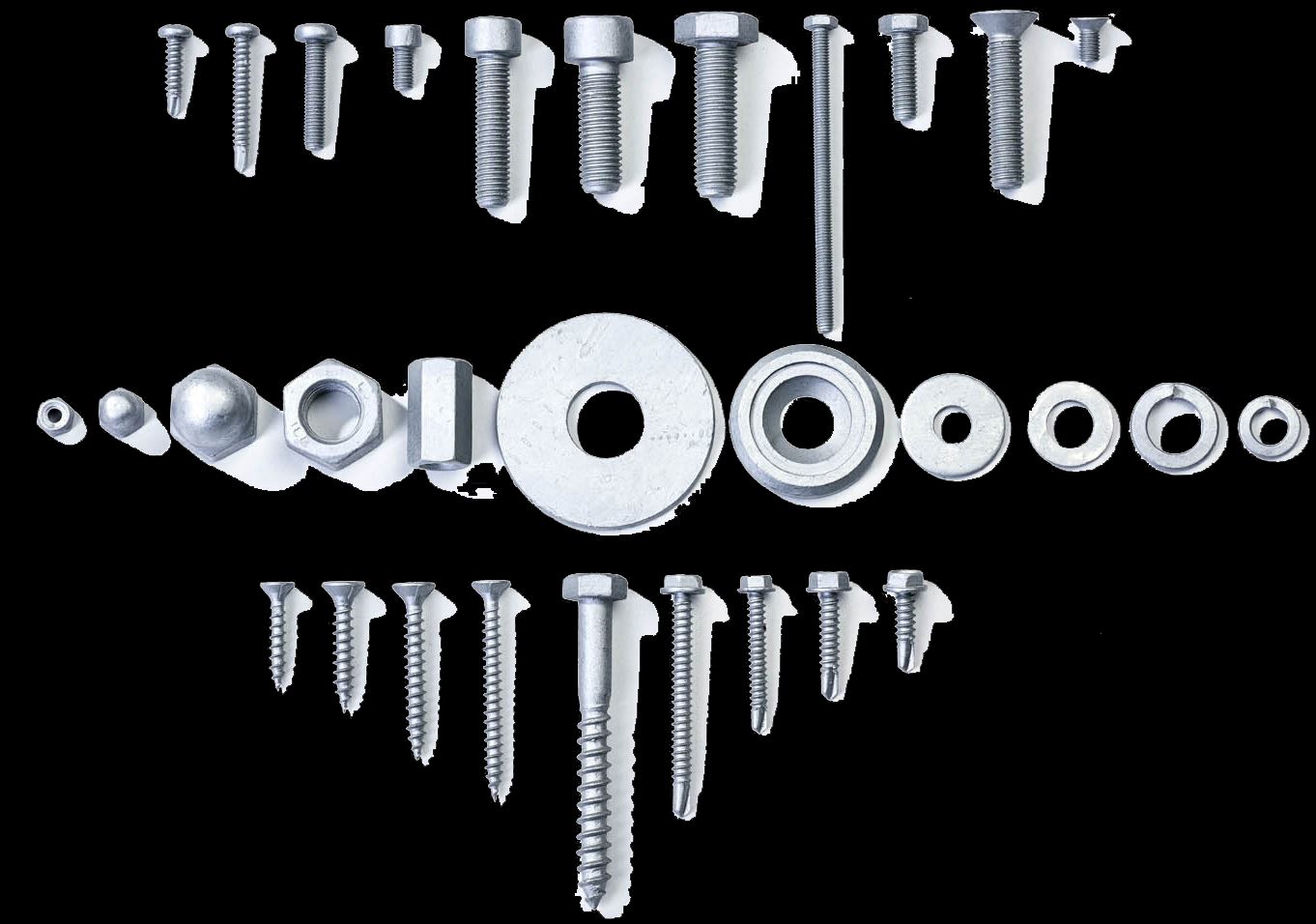
More than 15 years fastener coating specialist
ANY SURFACE TREATMENT POSSIBLE
Online you are able to order your most popular fasteners, daily we add new articles. But we can request the manufacturer the designated surface treatment for your application. Coated screws, bolts nuts, for any application. Contact us to meet a specialist for your fastener surface treatment advise.
What are popular surface treatments
Please find below the most popular surface treatments in the market:
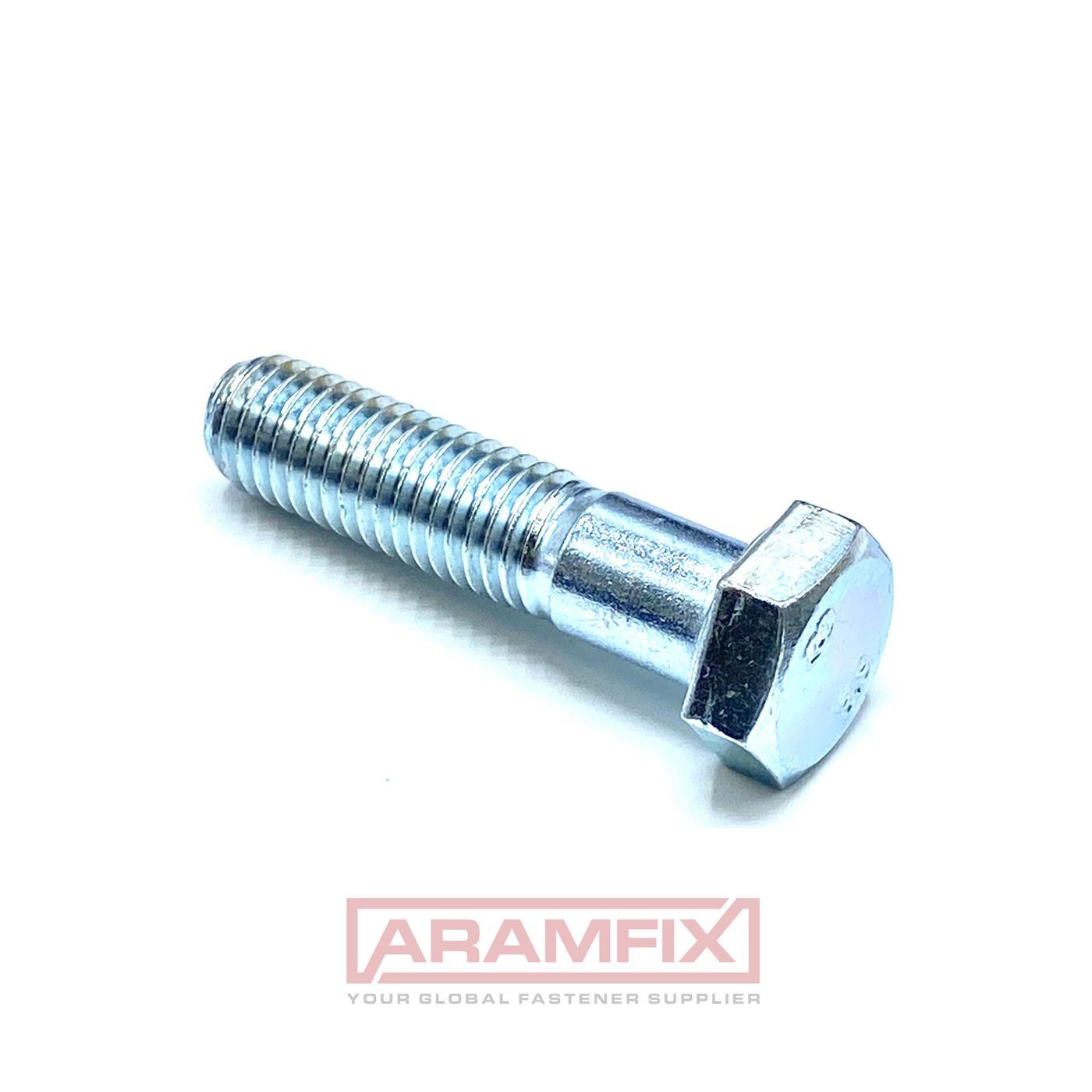
ZINC PLATING
Standard bright blue or white zinc plating is common worldwide used for many fastener applications. With a basic corrosion protection of 24hours SaltSprayTest it gives many applications for inside use. Typical layer thickness approx 3-5 microns.
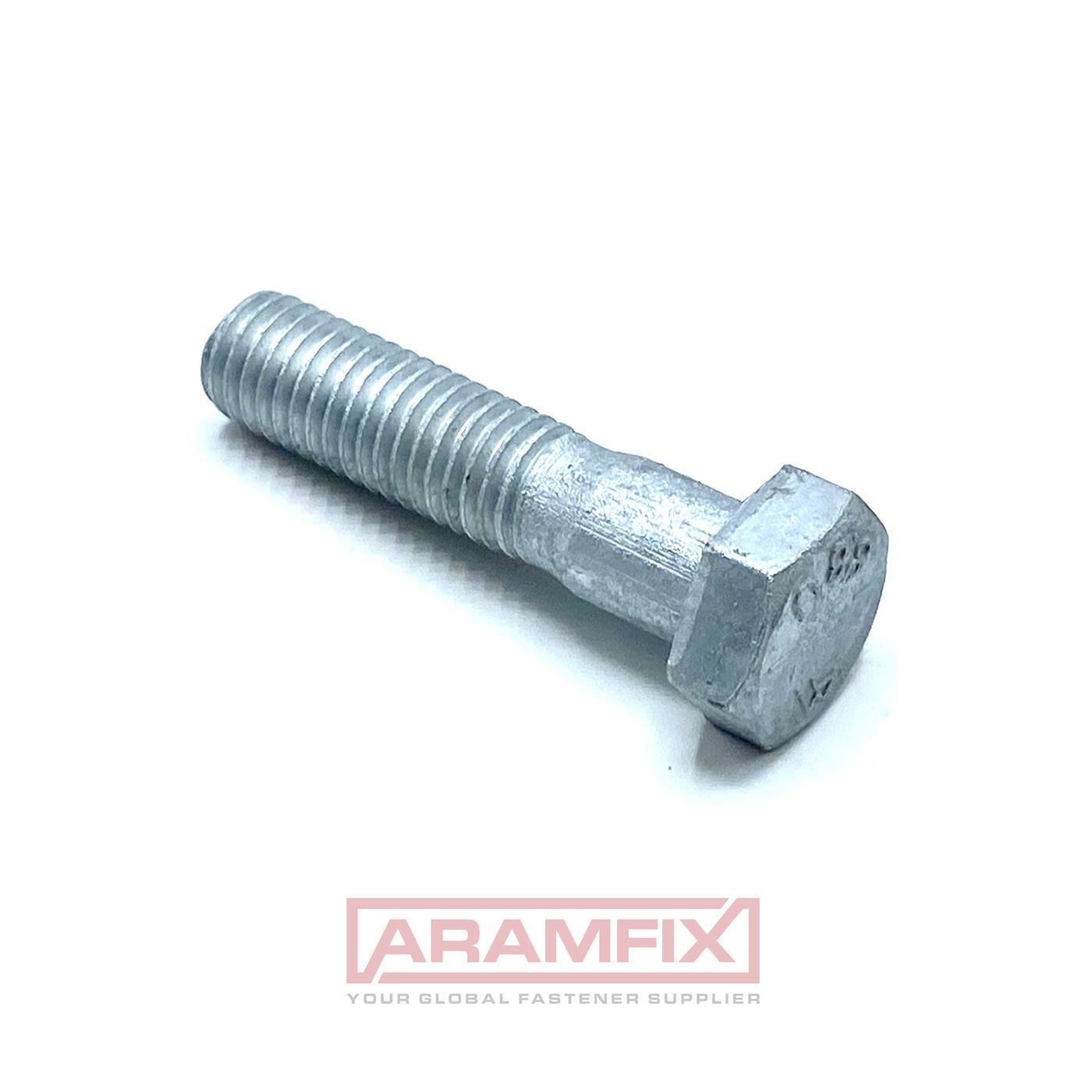
HOT DIP GALVANISING
When large constructions are hot dip galvansised often fasteners are also HDG threated. A layer of molten pure zinc in a thick layer gives great outdoor corrosion resistance. Not suitable for coastal shore area or high humidity. Typical layer thickness min 20 microns.
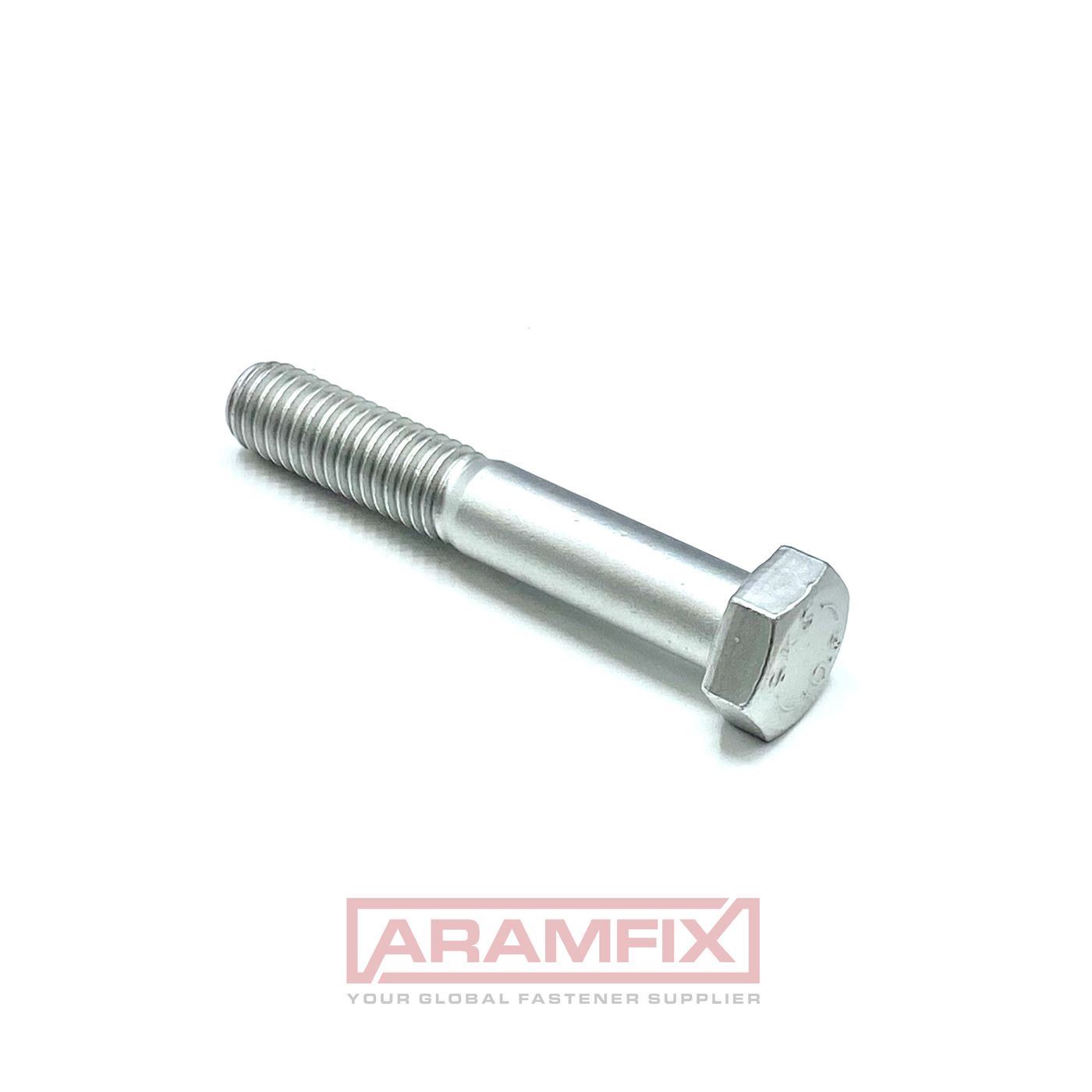
ZINC-FLAKE COATINGS
For high strength steel often zinc-flake coatings are used. There is no risk on hydrogen embrittlement so they can safely being used for steel grades with a tensile strength above 1000N/mm2. Typical layer thickness 6-10 microns.
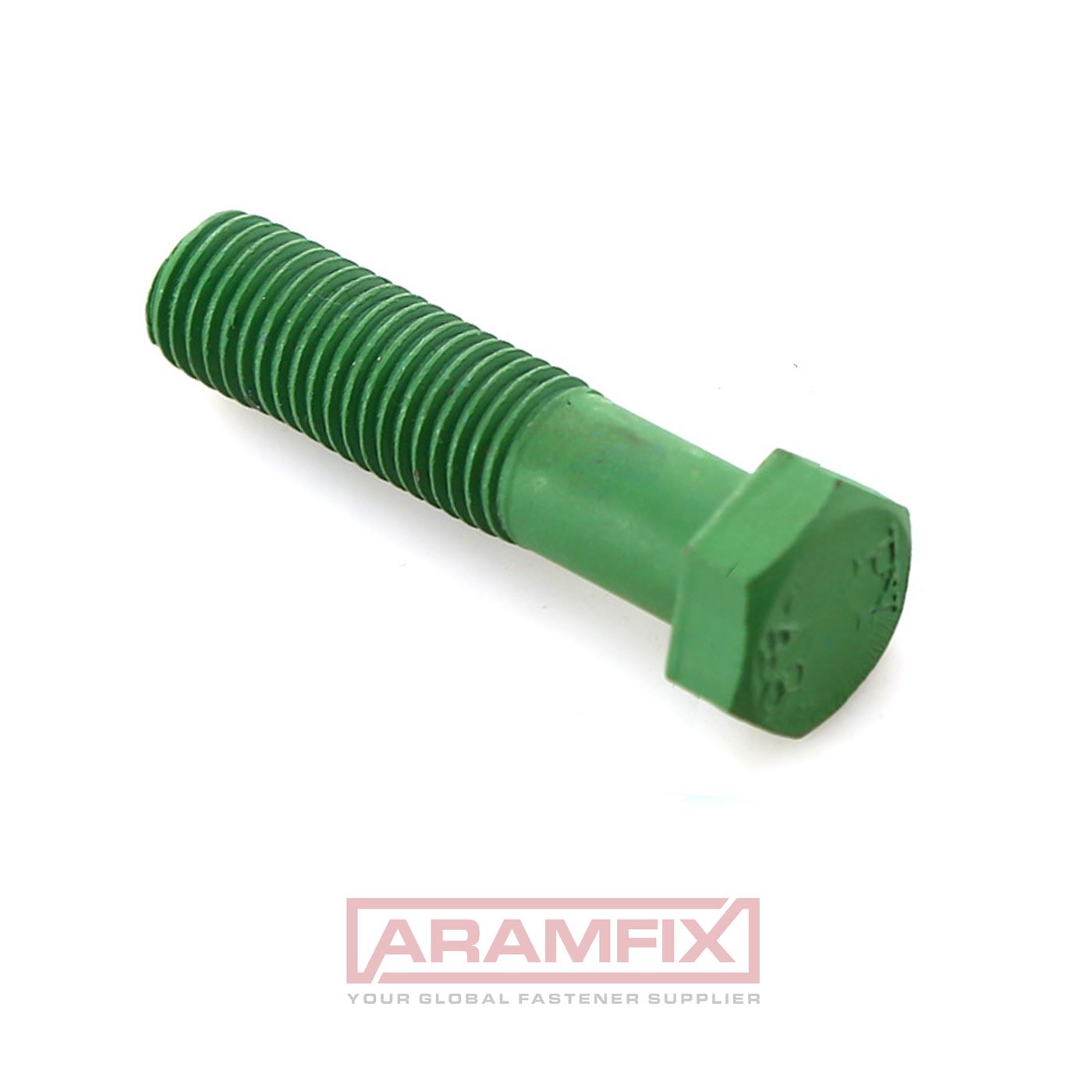
PTFE COATING
For offshore oil and gas industry often PTFE based topcoatings are used. They are in various colors available. With different base treatments a great variety of properties can be reached. Typical layer thickness above 20 microns.
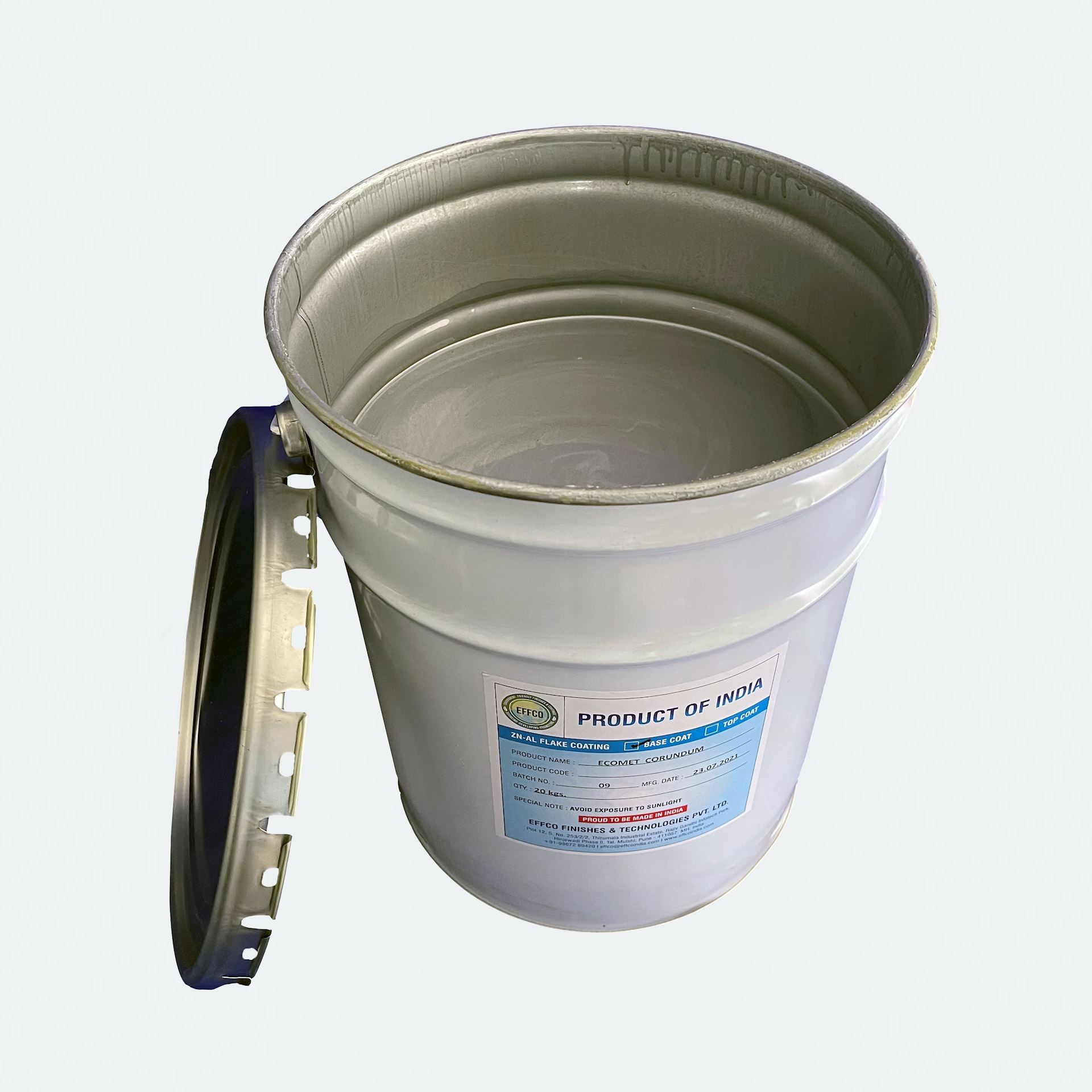
WITHOUT LICENCE
BUY ZINC-FLAKE COATING
Many Zinc-Flake coating manufacturers work with licencees. In every country there is one or some more job-coaters who may pay for the licence to buy their coating to apply commercially on fasteners. Since 2008 the Indian manufacurer EFFCO FINISHES & TECHNOLOGIES PVT. LTD. developed high corrosion resistant zinc-flake coatings water- or solvent-based. Now they have started to sell this licencee-free. To have this technology available for any manufacturer or as added value to small production batches. ARAMFIX made it possible to order online the products and equipment of EFFCO FINISHES & TECHNOLOGIES PVT. LTD.
Lorem ipsum dolor sit amet, consectetuer adipiscing elit. Aenean commodo ligula eget dolor. Aenean massa. Cum sociis natoque penatibus et magnis dis parturient montes, nascetur ridiculus mus.
Lorem ipsum dolor sit amet, consectetuer adipiscing elit. Aenean commodo ligula eget dolor. Aenean massa. Cum sociis natoque penatibus et magnis dis parturient montes, nascetur ridiculus mus.
Lorem ipsum dolor sit amet, consectetuer adipiscing elit. Aenean commodo ligula eget dolor. Aenean massa. Cum sociis natoque penatibus et magnis dis parturient montes, nascetur ridiculus mus.
Lorem ipsum dolor sit amet, consectetuer adipiscing elit. Aenean commodo ligula eget dolor. Aenean massa. Cum sociis natoque penatibus et magnis dis parturient montes, nascetur ridiculus mus.
Lorem ipsum dolor sit amet, consectetuer adipiscing elit. Aenean commodo ligula eget dolor. Aenean massa. Cum sociis natoque penatibus et magnis dis parturient montes, nascetur ridiculus mus.
Lorem ipsum dolor sit amet, consectetuer adipiscing elit. Aenean commodo ligula eget dolor. Aenean massa. Cum sociis natoque penatibus et magnis dis parturient montes, nascetur ridiculus mus.
Lorem ipsum dolor sit amet, consectetuer adipiscing elit. Aenean commodo ligula eget dolor. Aenean massa. Cum sociis natoque penatibus et magnis dis parturient montes, nascetur ridiculus mus.
ECO- CONSCIOUS
POWERFUL Dip-Spin Coater
each designed and manufactured to provide laboratories with a highly efficient and accurate means of applying uniform coatings
We’ll collaborate with your team and engineers to develop the optimal coating for your items to meet your exact specifications and standards.
- Economical method for bulk processing small parts such as fasteners, nuts, bolts, stampings, and springs.
- Repeatable when even coverage is required, like for threaded parts.
- Well-suited for high-production coating.
- Transfer efficiency is high, normally 98% or more.
- We can efficiently combine multiple combinations of coatings.
This automated, eco-friendly process guarantees consistent coverage, prevents hydrogen embrittlement, and enhances the longevity and reliability of every fastener we supply.
Where innovation meets industrial precision.
Lorem ipsum dolor sit amet, consectetuer adipiscing elit. Aenean commodo ligula eget dolor. Aenean massa. Cum sociis natoque penatibus et magnis dis parturient montes, nascetur ridiculus mus.
Lorem ipsum dolor sit amet, consectetuer adipiscing elit. Aenean commodo ligula eget dolor. Aenean massa. Cum sociis natoque penatibus et magnis dis parturient montes, nascetur ridiculus mus.
IN-HOUSE PRODUCTION
SEMI AND FULLY AUTOMATED DIP SPIN MACHINERY
Want to gain full control of your coating process? We provide everything you need, from expert training to full technical integration.
Our system has been tested by major OEMs to deliver the highest quality in large batches.
- Unique protection for extreme conditions
- Thickness- thinner than a single strand of hair
- Full command of the process and efficiency
- For all industrial applications
Follow the future of Zinc Flake Coating Technology.
Contact us: info@aramfix.com